The Complete Guide to Common Boiler Problems (And Repair Costs)
Is your boiler giving you a hard time? You’ve come to the right place. We’ve spent hours compiling the most common boiler problems for models from Worcester Bosch, Vaillant, Baxi, Ferroli, Ariston, Potterton, Vokera, and Glow-Worm.
Below, you’ll find the underlying causes behind most common boiler issues, ways of fixing them, and the associated repair costs.
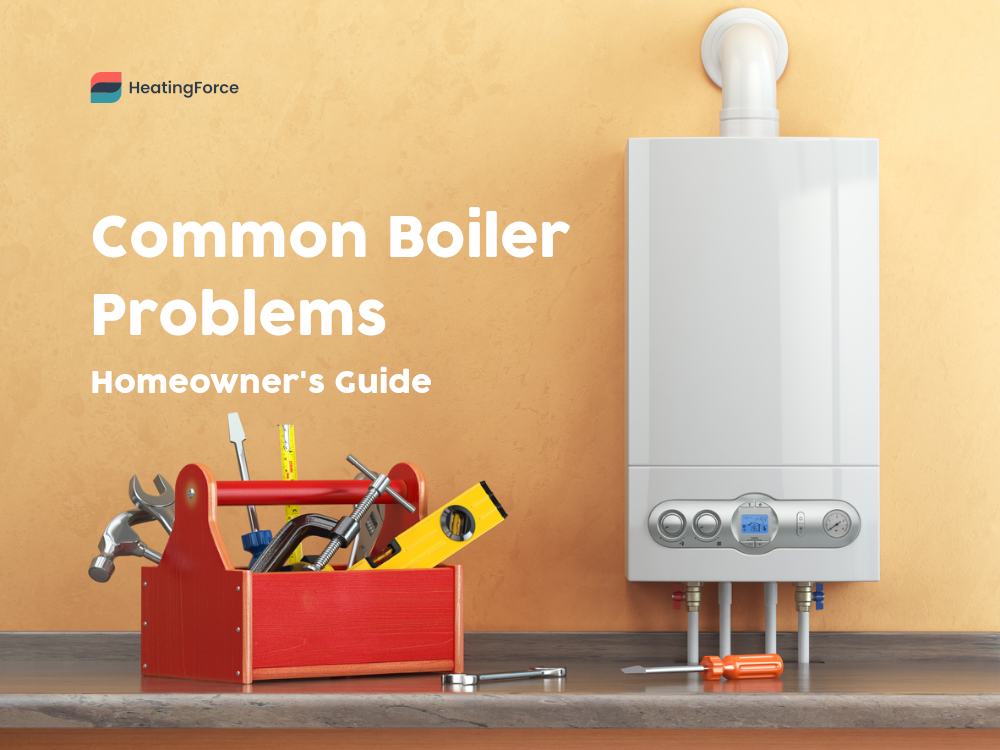
After troubleshooting boiler issues, sometimes there is more to a problem than meets the eye. It’s important not to jump to conclusions before getting a professional assessment of your boiler problem.
Work should always be carried out by an expert. Please check Gas Safe registration numbers before agreeing to have work completed.
Worcester Bosch (Post-2004 Models) – Common Boiler Problems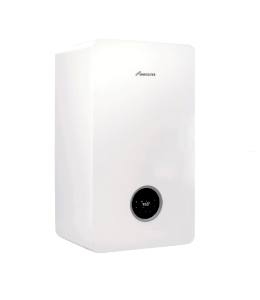
If your boiler was installed after 2004, it’s likely a Greenstar.
The broader Greenstar range includes the i, Si Compact, i System, CDi Megaflow, CDi, GB162, CDi FS Regular, Ri, 4000, and 8000 ranges. Below, we’ll cover faults that frequently occur in these models.
For an in-depth look at Worcester boiler faults, read our guide here.
Problem 1: Boiler Pressure Too Low
Most boilers operate with a water pressure of 1-3 bar. If the boiler pressure gauge shows a reading that’s below or above this range, the boiler won’t function correctly. More importantly, pressure that’s too low or high points to a problem, either with the boiler itself or the central heating system.
Low boiler pressure may be caused by:
- Leaking radiators, towel rails, or radiator valves, or other parts of the central heating system
- Boiler leak from components such as the pressure valve
- Automatic air vent needs replacing
- Condensate pipe is blocked (in cold weather)
Fix – Water Leak
If a radiator or towel rail is split, you’ll need a plumber to replace it.
If radiator valves are leaking, sometimes you can fix them by tightening up the nut slightly. In most cases, the valve has been displaced and the easiest option is to change the valve.
You can isolate the leaking radiator by turning the lockshield valve off completely. The water flow will then bypass this unit until the problem is fixed.
There’s also a chance that one of the boiler’s components — such as a pump seal or the pressure relief valve — is leaking water. If this is the case, you’ll need a Gas Safe heating engineer to assess the situation.
Fix – Automatic Air Vent Fault
When air collects in a system, it creates noise. An automatic air vent can remove this problem. However, there’s a good chance it’s leaked, seized, and now requires replacement.
You can usually remove an air vent via a quick release pin after draining down the system. The system will then need to be refilled and tested before you install a new vent.
Fix – Condensate Blockage
If pouring warm water on the condensate blockage doesn’t fix the issue, the problem is further up the line (potentially the trap or sump), and will require disassembly.
Repair Estimate
Fit new TRV (Thermostatic Radiator Valve): £25-40 each
Replace automatic air vent: £50-200
Remove condense blockage: £50-250
Troubleshoot a boiler losing pressure: £120-350
Problem 2: Flame Dies During Operation
When you Worcester’s flame goes out during operation, you’ll likely see the EA 229 fault code on the display.
This fault may be caused by:
- Excessive wind entering the flue
- The sump or condensate trap being blocked
Fix – Wind in the Flue
Install a branded Worcester Bosch plume management kit. This allows you to direct waste gas from the flue in any way you want, ideally in a direction where wind can’t enter the flue.
Fix – Condense Pipe Blockage
The pipe has likely frozen. You can try to melt the ice using a bucket of warm water. Don’t use hot water as it might crack the condensate pipe. If this method doesn’t remove the blockage, you might need an engineer to come and assess the problem.
Repair Estimate
Install a Worcester Bosch plume management kit: £180-250
Remove condense blockage: free/£50-250
Problem 3: Boiler Won’t Ignite (fault codes EA 227 and EA 261)
The boiler goes through its start up sequence followed by a ticking noise — that’s the sound of it trying to ignite — but fails to ignite. Fault codes EA 227 and EA 261 usually point to an ignition failure.
An ignition failure may occur because:
- There’s no gas supply
- Ignition leads are faulty
Fix – No Gas Supply
If you are on a meter, check whether you have credit; there should be an emergency credit option from your gas supplier if you’ve run out.
However, if you have just moved into the property, it’s likely that the gas was turned off — especially if the property was purchased on vacant possession. My advice would be to get a Gas Safe registered engineer to come and turn on the gas, and also to run a test for leaks.
Fix – Ignition Leads
If a Gas Safe registered engineer can isolate the problem to ignition leads, it’s simple enough to replace them with new ones.
Repair Estimate
Turn on gas and run a leak test (including minor repairs): £60-150
Replacement of ignition leads: £160-200
Replace probes and ignition leads: £200-400
Problem 4: Knocking Noises From the Boiler
If you have a noisy boiler that keeps producing knocking sounds, you’ll mostly hear the noise when you first switch the boiler on.
Such a noise usually occurs because there’s an issue with the gas valve or fan.
Fix – Gas valve and fan
There is no simple fix. The most likely cause could be that the gas valve and fan are running out of sync. This could be an issue with the gas valve, the fan, or both. Either way, you’ll need a Gas Safe engineer to diagnose the fault.
Repair Estimate
- Install new gas valve: £150-500
- Install new fan: £200-600

Worcester Bosch (Pre-2004 Models) – Common Boiler Problems
If your Worcester boiler is not a Greenstar, it was likely made before 2004. Here are the common gas boiler issues you may experience.
Problem 1: Boiler Will Not Ignite
This assumes the boiler has gone through all the usual start up procedures (no additional knocks or unusual noises compared to usual). The fan will begin to spin in anticipation of the boiler igniting, but it fails to do so.
Here’s why the boiler may fail to ignite:
- Air pressure switch is not functioning correctly
- Fan has stopped working
Fix – Air Pressure Switch
Replacing the air pressure switch is the most straightforward approach.
In some cases, the piping leading to the air pressure switch may degrade over time. Replace these pipes alongside the switch.
Fix – Fan
If your boiler doesn’t go through the normal start up sequence (i.e. you can’t hear the fan running) there’s a good chance the fan is your problem.
It might be seized, but as most boiler fans have a sealed bearing unit, trying to unseize the bearings using external lubricant won’t work.
Depending on the age of the boiler and cost, the best option is usually to replace the boiler all together, especially if there are other problems and no warranty coverage.
Repair Estimate
Install new air pressure switch: £100-250
Install new fan: £200-600
Problem 2: Boiler Keeps Locking Out
There are 2 possible reasons why the boiler is not producing heating or hot water:
- The boiler keeps locking out
- There’s an ignition failure, followed by a boiler lockout
Fix – Boiler Locks Out Before It Tries to Start Up
This boiler issue is usually electrical. The PCB (printed circuit board) is the “brain” of your boiler, and is likely the culprit and needs to be replaced. You may want to consider getting a new boiler if you need a new PCB and your old boiler is out of warranty.
Fix – Boiler Tries to Ignite, Then Locks Out
Each boiler contains probes and ignition leads, which are needed for ignition to take place. It’s likely these have degraded over time and need to be replaced.
Repair Estimate
Install a new PCB: £250-500
Replace probes and ignition leads: £200-400
Problem 3: No Heating and Hot Water, but Boiler Is Energised
Many old Worcester boilers were fitted with overheat thermostats to monitor the boiler for overheating. If such a thermostat malfunctions, it could disrupt your boiler’s operations.
Fix – Overheat Thermostat
The obvious answer is going to be a direct replacement. To check this isn’t a onetime issue, it’s worth running a system reset before replacing the thermostat.
Repair Estimate
Installation of a new overheat thermostat: £150-320
Problem 4: Low Water Temperature
If the lights on the boiler are showing that it’s getting up to temperature, but the water itself isn’t, the heat exchanger is probably not working correctly.
Fix – Heat Exchanger
A Gas Safe engineer will have to determine whether the heat exchanger can be fixed. If not, then you’ll have to pay for repairs.
Repair Estimate
New heat exchanger: £400-650
Baxi – Common Boiler Problems
Below are the boiler problems you’re most likely to encounter if you’ve got a Baxi boiler; read here to get our full guide.
Problem 1: Boiler Lockout (common on Solo 1PF and 2PF)
The most common reason a lockout happens is due to overheating. This, in turn, may be caused by:
- Low boiler pressure
- Faulty overheat thermostat
- Blockages (especially during colder months)
Fix – Low Boiler Pressure
You can top up boiler pressure with the filling loop. Be warned: the higher the running temperature of your Baxi, the higher the pressure will be. So, the pressure may look low when the boiler is off (or not on full power), but will increase as the hot water heats up.
Fix – Overheat Thermostat
To check this isn’t a onetime occurrence, reset the thermostat; both the 1PF and 2PF have a reset sequence. If this doesn’t help, you’ll have to replace the faulty thermostat.
Fix – Blockages
The most common blockage is in the condense pipe. In winter months, freezes and blocks the flow. If the pipe is accessible, pouring warm water over the pipe is usually enough to remove the blockage. If this doesn’t clear the blockage, there’s likely an obstruction further up, in the condensate trap or the sump.
Repair Estimate
New overheat thermostat: £150-320
Remove condensate blockage: £50-250
Problem 2: Boiler Leak
Leaks are particularly common for the Baxi 30HE, 105HE, 133HE and Duo Tech combis. They mostly happen due to faulty housing for the diverter valve and pump.
Fix – Replace the Housing
The housing degrades over time, eventually causing boilers to leak water. Replacing the housing is not a particularly easy job.
*Quick Tip: It’s worth spending an extra hour assessing potential water damage to other boiler parts while the boiler casing is removed.
Repair Estimate
Replacement of diverter valve housing: £100-150
Replacement of diverter valve (including housing): £250-380
Problem 3: Banging and Knocking Noises
These noises occur regularly with the Duo Tech and HE ranges, and is usually caused by restricted water flow, which can affect boilers and other components of heating systems, like the pipework.
Fix – Restricted Flow
If this problem has just started, the circulator pump could be failing. A replacement is the easiest way to resolve heating pump problems.
However, if restricted flow (and banging) has always been a problem, the pipework may be incorrectly installed or blocked. As an example, we went to a property where 10mm pipework (which actually should have been 15mm) was incorrectly routed.
Newer pumps tend to have configurable flow rate settings (from 1-3 on the basic Grundfos range). You can turn down the flow range on the head of the pump.
Repair Estimate
Replace pump (Grundfos): £240-380
Problem 4: Boiler Won’t Ignite Correctly
Models most likely to suffer are the Baxi Barcelona and the 100E. Leaking seals are the most common cause.
The combustion chamber seals on the 100E and Barcelona can degrade and then start leaking with time. The boiler will sense a leak and lock out.
Fix – Leaking Seals
The seals will need to be changed. In some cases, it makes sense to change the whole combustion chamber.
Repair Estimate
Fix leaking seals/replace combustion chamber: £200/£550
Problem 5: No Hot Water From a Combination Boiler (Unless Heating Is On)
This is a common problem with the 80E and 105E combi boiler models, and is usually caused by a faulty diaphragm.
Fix – Diaphragm
If the diaphragm is faulty, you’ll need to replace it. As this is a time consuming job, it often makes sense to change the diverter valve altogether.
Note that the diverter valve may also be responsible if there’s hot water but no heating.
Now, if there’s no heat OR hot water, your boiler has likely locked out, or isn’t able to ignite.
Repair Estimate
Replace diaphragm (and diverter valve): £250-380
Ferroli – Common Boiler Problems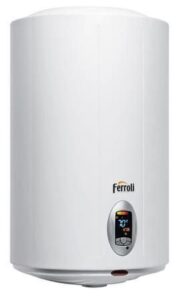
Below are the most common issues you may run into as a Ferroli owner.
Read our full guide to Ferroli boiler faults for more information.
Problem 1: Boiler Leak
Leaks are a common problem on the 30C model. Potential causes behind a boiler leak include:
- Faulty or loose pump
- Faulty shutoff valve
Fix – Leaky Pump
Visually check the pump to see if it’s leaking. If it is, check whether the pump is rock solid in its housing. Should you find that it’s a bit loose, locate the screws/Allen key bolts that are securing them to the boiler and tighten them.
If the pump is still leaking, it’s likely due to a blown seal. In this case, it’s usually wise to replace the entire pump.
Reducing the pump’s flow rate is a temporary fix that sometimes works. Doing so will put less pressure on the seal and should reduce the severity of the leak.
Fix – Faulty Shut-Off Valve
Faulty shut-off valves are rarely fixed; you’ll likely need a replacement.
Repair Estimate
Replace pump (Grundfos): £240-380
Install new shut-off valve: £90-150
Problem 2: Low Pressure
A possible cause of low pressure is that the expansion vessel needs to be repressurised.
Fix – Expansion Vessel
You can adjust the pressure using a pump. However, there’s a good chance you may need a new expansion vessel altogether.
Repair Estimate
Fitting a new expansion vessel: £175-250
Problem 3: Boiler Keeps Switching On and Off Sporadically
The boiler doesn’t come on when you set it to, and vice versa. Or, you’ve got a boiler not responding to thermostat commands.
Potential cause:
- Mechanical timer is faulty
- Malfunctioning thermostat
Fix – New Mechanical Timer
Replace the existing mechanical timer. They are easy to pick up from heating spares suppliers.
Fix — New Thermostat
Replacing your thermostat with a new, smart or programmable version can not only fix the boiler problem at hand, but also help you reduce energy waste.
Repair Estimate
New mechanical timer: £90-150 (depending on brand)
New thermostat: £100-£300 (depending on brand)
Problem 4: Boiler Locked Out
This issue is most common on the Ferroli Modena and Falcon ranges, and a faulty PCB is the most likely cause.
Fix – PCB
The obvious answer is a PCB replacement.
Before jumping to conclusions, test the PCB with a digital multi-meter.
PCB replacements are not cheap. If a boiler is over 10 years old, boiler replacement is usually the most cost effective option.
Repair Estimate
Replace PCB: £250-500
What kind of fuel does your boiler use?
Fixed price online with next day installation
Vaillant – Common Boiler Problems
Vaillant make excellent boilers, but even these fail from time to time. Below are their most common errors; have a read through our guide here for a more thorough look at Vaillant boiler problems.
Problem 1: Low of Boiler Pressure (fault code F22)
Low pressure is a common issue with the Vaillant Eco-Tec 24, 28, and 624 models, and is usually indicated by the F22 fault code.
If this happens, it’s possible that the boiler has lost pressure over time and needs to be topped up.
Fix – Low pressure
Most combination boilers have an external filling loop (a braided hose). There’s a handle on this hose; turning the handle will top up the boiler pressure.
Don’t overfill the boiler. Boiler pressure will rise as it heats up and too much pressure can put unwanted stress on internal components.
Problem 2: F75 Error Code
Vaillant’s Eco-Tec are prone to the F75 fault code appearing. A faulty pump or pressure sensor are the likeliest culprits.
Fix – Pump
Vaillant used to have Wilo pumps in their Eco-Tec range. These were low-quality pumps, and they’ve since been upgraded to Grundfos.
If you’ve noticed leaks, the pump is the culprit and the easier option is to get a replacement (from a better known brand like Grundfos).
Fix – Pressure sensor
The F75 fault relates to both the pressure sensor and the pump. If your pump is running but the code is still flashing, it’s likely the pressure sensor.
In this case, replace the sensor. If it’s dirty or blocked, think about running a hot flush through the system and adding a magnetic system filter (this will prevent this problem from happening again).
Repair Estimate
Replace pump (Grundfos): £240-380
Install new pressure sensor: £130-£180
Hot flush: £150-350
Click for further details on the Vaillant F75 fault code.
Ariston – Common Boiler Problems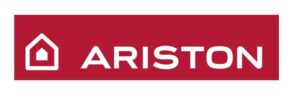
If you’ve got an Ariston, you’re most likely to experience the faults listed below. For a more comprehensive guide to Ariston boiler problems, have a read here.
Problem 1: Boiler Won’t Ignite (Fault Code A1)
This fault is most common on the Ariston Microgenus 24HE and 28HE models. The most probable causes are:
- Faulty ignition leads
- Lack of gas supply
Fix – Faulty Ignition Leads
Check for current using a multi-meter. If there is no current, replace the ignition leads.
Fix — Gas Supply Issues
If your other gas appliances aren’t working, your gas supply has probably been shut off. Get in touch with the supplier to sort out the issue.
Problem 2: Low pressure (Fault Code E2)
This fault is common on the Microgenus 30HE. A boiler losing pressure could have air trapped in the system, or experience expansion vessel leakage.
Fix – Low Pressure
The quick fix is to top up the boiler using the external filling loop. Top up to roughly 1.5 bar.
You’ll need a Gas Safe engineer to diagnose and fix the fault.
Repair Estimate
Replace probes and ignition leads: £200-400
Problem 3: Fault Code E34 On Display
Many old Ariston Microgenus boilers are affected by this fault code. And, a faulty air pressure switch is a possible root cause.
Fix – Air Pressure Switch
Simply replace the air pressure switch.
Problem 5: Fault Code A41
This problem occurs mainly on the newer, Microgenus 2 range; namely, the 24 RFFI model, and is often caused by a faulty fan.
Fix – Fan
Using a multi-meter, check whether the fan has current. If no current shows up, perform the same check on the PCB.
If the reading from the PCB is fine, the fan needs replacing. However, if the PCB isn’t showing a reading, it’s likely the PCB needs replacing. Generally speaking, replacing the PCB is extremely costly, so boiler replacement is usually the better option.
Repair Estimate
Install new air pressure switch: £100-250
Install new fan: £200-600
Vokera – Common Boiler Problems
Here are some errors you might run into if you’ve got a Vokera boiler in your home.
For a full list of Vokera problems, check out this guide.
Problem 1: Fault Codes 92/93 and 95
This occurs in extremely cold weather, when ice blocks the condensate pipe.
Fix – Condensate Blockage
Using lukewarm water, try and melt the ice inside the condensate pipe, then reset the boiler before switching the heating back on; the system should clear the fault.
If this doesn’t work, the blockage is likely more severe and you’ll need a Gas Safe engineer’s assistance.
Repair Estimate
Troubleshoot and fix condense blockage: £100-250
Problem 2: Ignition Problems
This has been particularly common with the Vokera Compact 25HE (fault code A01) and the Vokera Linea24 HE. The problem may stem from a faulty gas valve or PCB.
Fix – Gas Valve
You can use a multimeter to see if there is current to the gas valve. If there is no current, the gas valve and solenoid will need replacing.
Fix – PCB
If the PCB is dead and needs replacing, especially if other parts are worn, a replacement boiler might make more sense.
Repair Estimate
New gas valve fitted: £180-300
Replace PCB: £250-500
Replacement boiler: you can get a quote by filling in this form.

Problem 3: Low Pressure
Low boiler pressure is an extremely common problem with all boilers, not just Vokera’s. A leak somewhere in the system is probably responsible for the dip in pressure.
Fix – Leaky Boiler/Central Heating System
The leak may affect any of the boiler’s components, or any other parts of the heating system. If you’re unable to find the leak yourself, you’ll need a Gas Safe engineer to do this for you.
Once the leak has been fixed, you can repressurise the boiler using the filling loop.
Repair Estimate
Troubleshoot and fix pressure loss: £120-350
Problem 4: Hot Water Doesn’t Work/Only Works With Heating On
This is common with the Vokera Vision and Flowmatic ranges. When there’s no hot water unless the central heating is on, you’ve probably got a diverter valve fault on your hands.
Fix – Diverter Valve
On some occasions, it’s just the diaphragm washer that needs replacing. If swapping out the washer on the valve doesn’t solve the problem, the whole diverter valve will need to be replaced.
Repair Estimate
Replace diaphragm (and diverter valve): £250-380
Glow Worm – Common Boiler Problems
Below, we’ve listed the issues that are common to Glow Worm boilers.
For a complete explanation of Glow Worm faults, please read our in-depth guide here.
Problem 1: Flame Not Detected
You’ll get this on Ci models when a F16 fault code appears. Possible causes include:
- Faulty probe
- Pilot light keeps going off/won’t light
Fix – Faulty Probe
Most likely, sludge build-up in the system has clogged up the probe. You’ll need to remove and clean it. If the problem persists, you’ll have to replace the probe and lead.
Fix – Pilot Light Not Working Properly
If the probe is clean, the pilot light assembly may be jamming. You’ll need a heating engineer to disassemble, clean, and reassemble the pilot light.
Repair Estimate
Replace probes and ignition leads: £200-400
Replace pilot assembly: £100-180
Problem 2: F9 Fault Code
The F9 fault code is common on the Glow-Worm Flexicom CX and the Ultracom HXI ranges. The likeliest underlying issue is sludge buildup.
Fix – Sludge Buildup
First, you’ll need to clean the system out. You can do so with a power flush, hot flush, or by manually draining down and hosing out the radiators.
After draining and cleaning the system, you should add inhibitor to the system and install a magnetic filter to catch debris. An engineer will clean the magnetic filter during your boiler service.
Repair Estimate
Hot flush: £150-350
Install magnetic system filter: £150-250
Problem 3: Flexicom CX Showing a F3 Fault Code
This error code is particularly common with the 30CX, and it’s caused by a faulty fan.
Fix – Fan
First, you’ll need to confirm the fault is with the fan. Use a multi-meter to check the current; you’ll have to trace back the connections from the PCB.
The fan can rarely be fixed, so replacing it is usually the only option.
Repair Estimate
Install new fan: £200-600
Problem 4: F61, F62, F63, F64, F65, and F67 Fault Codes on a Betacom
This is one of the most common fault codes on all the of Betacom boilers. Unfortunately, it’s caused by a part that’s notoriously expensive to replace — the PCB.
Fix – PCB
A faulty PCB is not good news. The part itself is incredibly expensive. With labour on top, it usually makes more sense to replace the old boiler.
That’s a last resort, though. Using a multimeter you can check to see if the fault is the whole PCB unit failing, or a piece of the PCB. It could be a loose connection, for instance.
Repair Estimate
Replace PCB: £250-500
Potterton – Common Boiler Problems
Problem 1: Leaky Boiler
This is a common fault on the Potterton Promax.
Possible causes include:
- Pump seal faulty
- Flow/pump switch faulty
Fix – Pump Seal
Remove the pump and replace the seal. If the boiler is particularly old, it might be worth replacing the whole pump unit.
Fix – Flow/Pump Switch
The leak is likely coming from the o-ring on the pump/flow switch. A quick fix would be to replace this o-ring; however, more often than not, it makes a lot more sense to replace the whole unit.
Repair Estimate
Replace pump (Grundfos): £240-380
Problem 2: Boiler Makes Banging Noises While Firing Up
This commonly happens on the Promax HE models when the burner is not working correctly.
Fix – Burner
Newer burners are now ceramic so they have fewer noise-related issues. Swapping out the old burner for a new ceramic one is a good approach to this issue.
Repair Estimate
Fit new burner: £280-400
Problem 3: Smell of Gas Near the Boiler
Switch your gas and boiler off straight away: there is probably a gas leak coming from the heat exchanger.
Unfortunately, this issue is all too common with Potterton HE models.
Fix – Ring a Gas Safe Engineer
This fault poses an imminent explosion hazard and requires immediate professional assessment.
Repair Estimate
Run leak test, identify leak/s and fix (including parts): £150-500
Considering a Replacement Boiler?
If you find yourself paying for repairs often, a replacement boiler is worth considering. We’ve created a guide to boiler replacement costs here, and you can also get a fixed price online from Heatable.
Heatable offer competitive prices and offer a price-match guarantee if you do find something better. Installation service is blazing fast–usually within 24 hours, and all installations come with an incredible 10-year warranty to boot.

What’s Next?
If your problem is not listed, please see our detailed article on heating and boiler problems here.
Have any questions? We’re happy to respond in the comments below.