Boiler Parts and Functions
A boiler part is a component that contributes to the system’s operation, safety, and efficiency. Each part plays a specific role in the boiler’s ability to heat water and distribute warmth throughout a home.
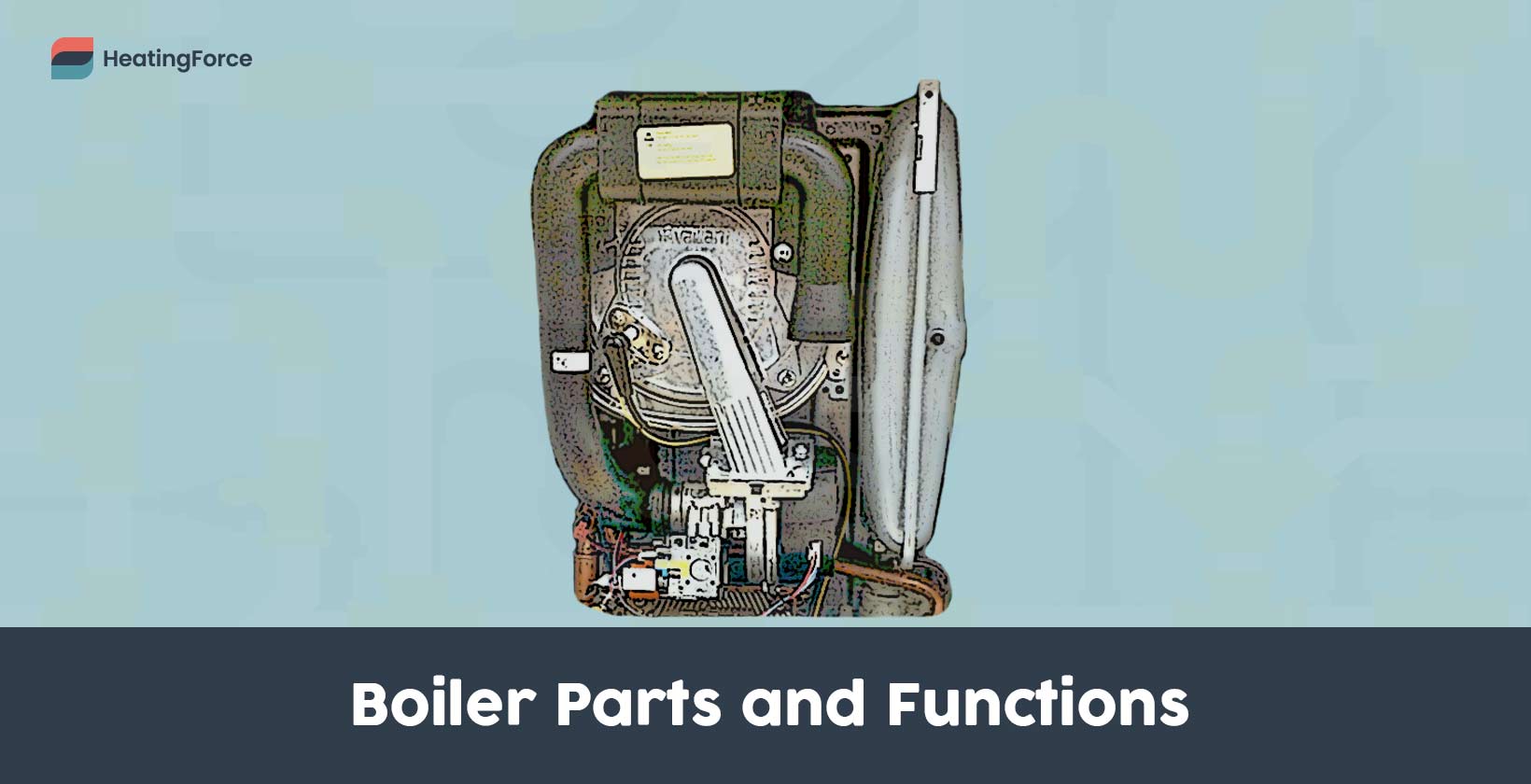
The list below provides an overview of the 26 most essential boiler parts and their primary functions.
- Burner: Ignites the boiler’s fuel, providing heat for the water.
- Heat exchanger: Transfers heat from the burner to the water inside the boiler.
- Combustion chamber: Where the fuel is burned to generate heat.
- Refractory: Heat-resistant material lining the combustion chamber to retain heat.
- Ignition system: Initiates the burner’s flame to start the heating process.
- Pilot light: A small, constant flame used to ignite the burner in some boilers.
- Expansion tank: Absorbs excess water pressure in the system.
- Controls: Allow users to regulate the boiler’s operation.
- Printed Circuit Board (PCB): The electronic system controlling the boiler’s functions.
- Timer: Sets the operational schedule of the boiler.
- Aquastats: Monitors and regulates water temperature in the boiler.
- Overheat thermostat: A safety device that shuts off the boiler if it gets too hot.
- Superheater: Increases steam temperature above its saturation point (not typically found in residential boilers).
- Circulator pump: Moves heated water from the boiler through the heating system.
- Economiser: Preheats incoming water using residual heat (more common in industrial boilers).
- Backflow valve: Prevents the reverse flow of water within the system.
- Pressure Release Valve (PRV): Releases excess pressure to prevent damage.
- Diverter valve: Directs hot water between the heating system and taps as needed.
- Auto-air vent: Releases trapped air in the system to maintain efficiency.
- Fan: Ensures safe expulsion of combustion gases via the flue.
- Exhaust stack (flue): Channels combustion gases from the boiler to the outside.
- Gas Valve: Regulates the flow of gas to the burner.
- Filling loop: Used to manually increase water pressure within the boiler.
- Supply lines: Pipes that deliver heated water from the boiler to the heating system.
- Return lines: Pipes that return cooled water back to the boiler for reheating.
- Condensate trap and drain: Collect and dispose of condensate generated during combustion.
The aforementioned parts work in unison as the boiler heats water and circulates it throughout the home’s radiators. Regular annual service of boiler components is essential for ensuring the safe and efficient operation of the boiler and adhering to its warranty requirements.
Below is a detailed overview of a boiler’s most essential parts, their functions, maintenance requirements, and replacement costs.
1. Burner
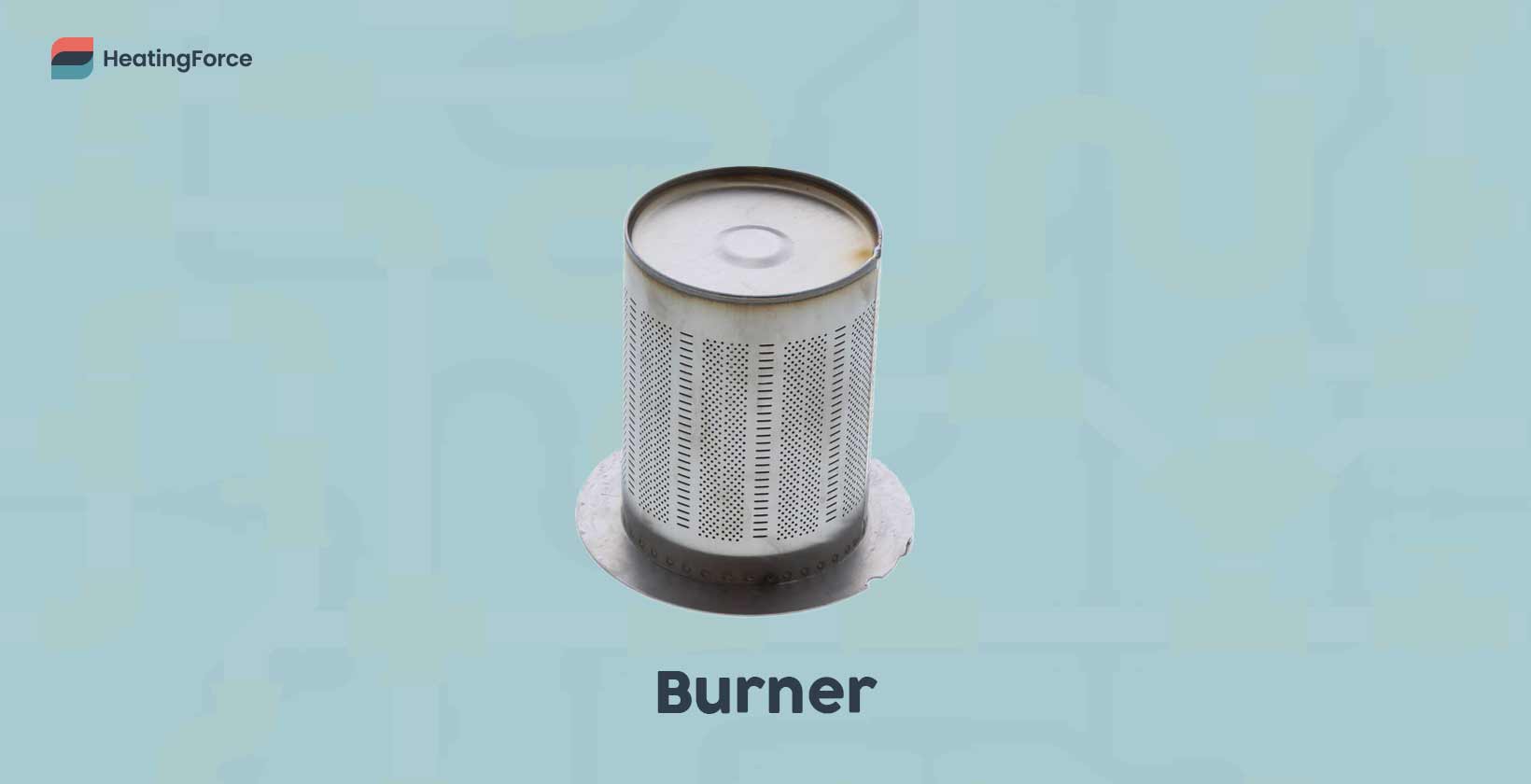
The burner is a critical boiler component responsible for mixing fuel with air, igniting it, and thus generating heat that then transfers to water. Gas boiler burners ignite gas or LPG, whilst burners in oil boilers combust kerosene. The burner’s function is central to the boiler’s operation since its efficiency influences the heating system’s performance and cost-effectiveness.
Regular burner maintenance (such as cleaning and damage inspection) is essential for ensuring optimal fuel use and consistent heat output. A burner with too much age-related wear and tear typically needs replacement to ensure that the boiler continues to operate safely and efficiently.
Replacement burners cost between £300 and £500 excluding labour. Sourcing spare gas boiler burners is not a challenge in the UK, as these are widely available at online and brick-and-mortar shops. On the other hand, oil boiler burners may be harder to find, especially for older models from lesser-known brands.
2. Heat exchanger
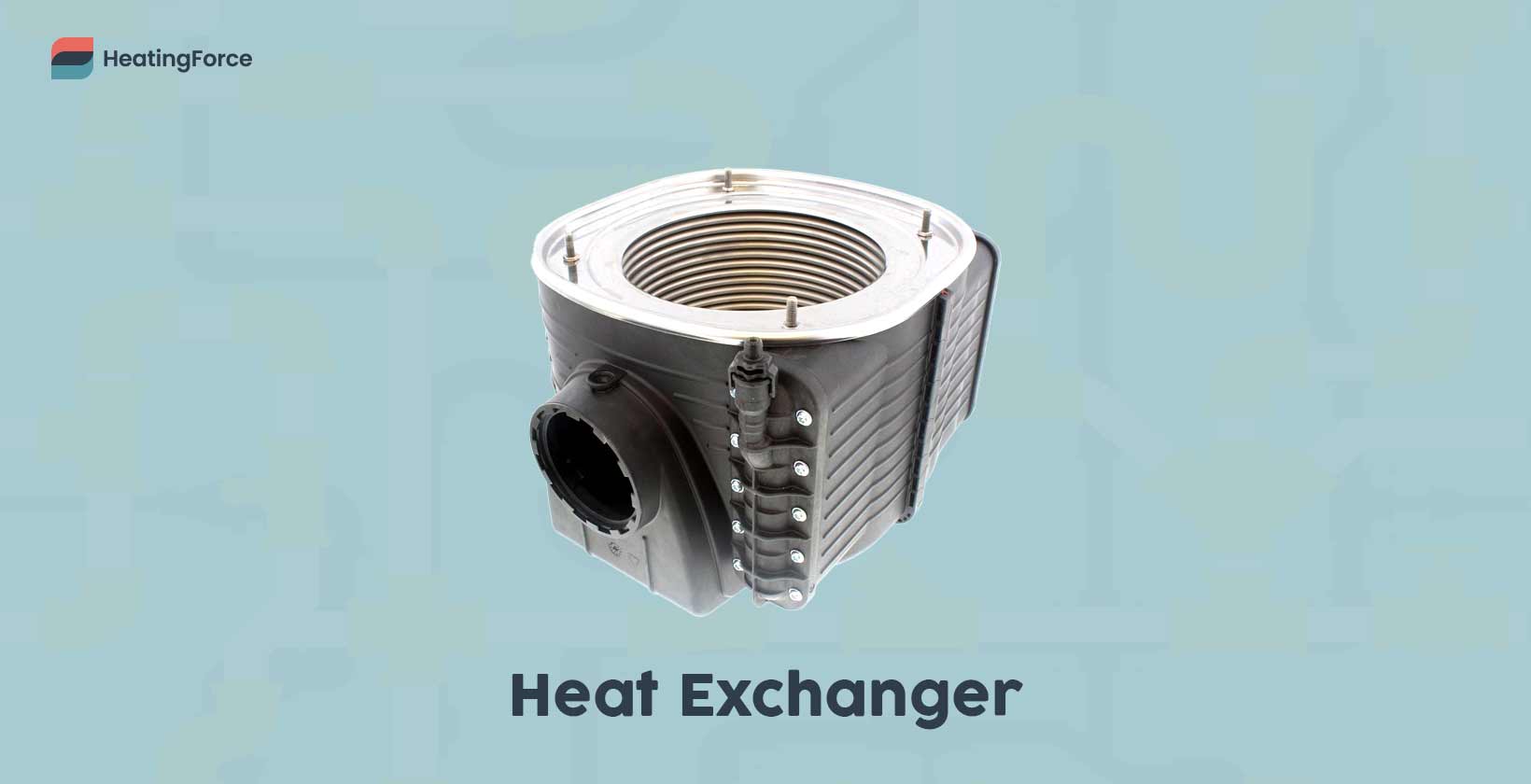
The boiler heat exchanger is an indispensable component that transfers the heat generated by the burner to the central heating and tap water. Its efficiency dictates the boiler’s ability to heat the home effectively.
The integrity of the heat exchanger is crucial to the boiler’s performance, so annual service and maintenance are paramount. The buildup of limescale or heating sludge impedes heat transfer, leading to boiler inefficiency and increased fuel costs. A heat exchanger with severe blockages may become irreparable, thus warranting a pricey replacement. To prevent the aforementioned issues, annual boiler service by a Gas Safe engineer (or OFTEC technician if you have an oil boiler) must involve a thorough inspection and cleanup of the heat exchanger.
A heat exchanger that’s beyond repair must be replaced, with costs generally ranging between £500- £700 without labour. Your local heating and plumbing merchants should have spare heat exchangers for the most common boiler brands. However, sourcing the spare part for more obscure brands and oil boilers may be more of a challenge, meaning that repairs might take longer.
3. Combustion chamber
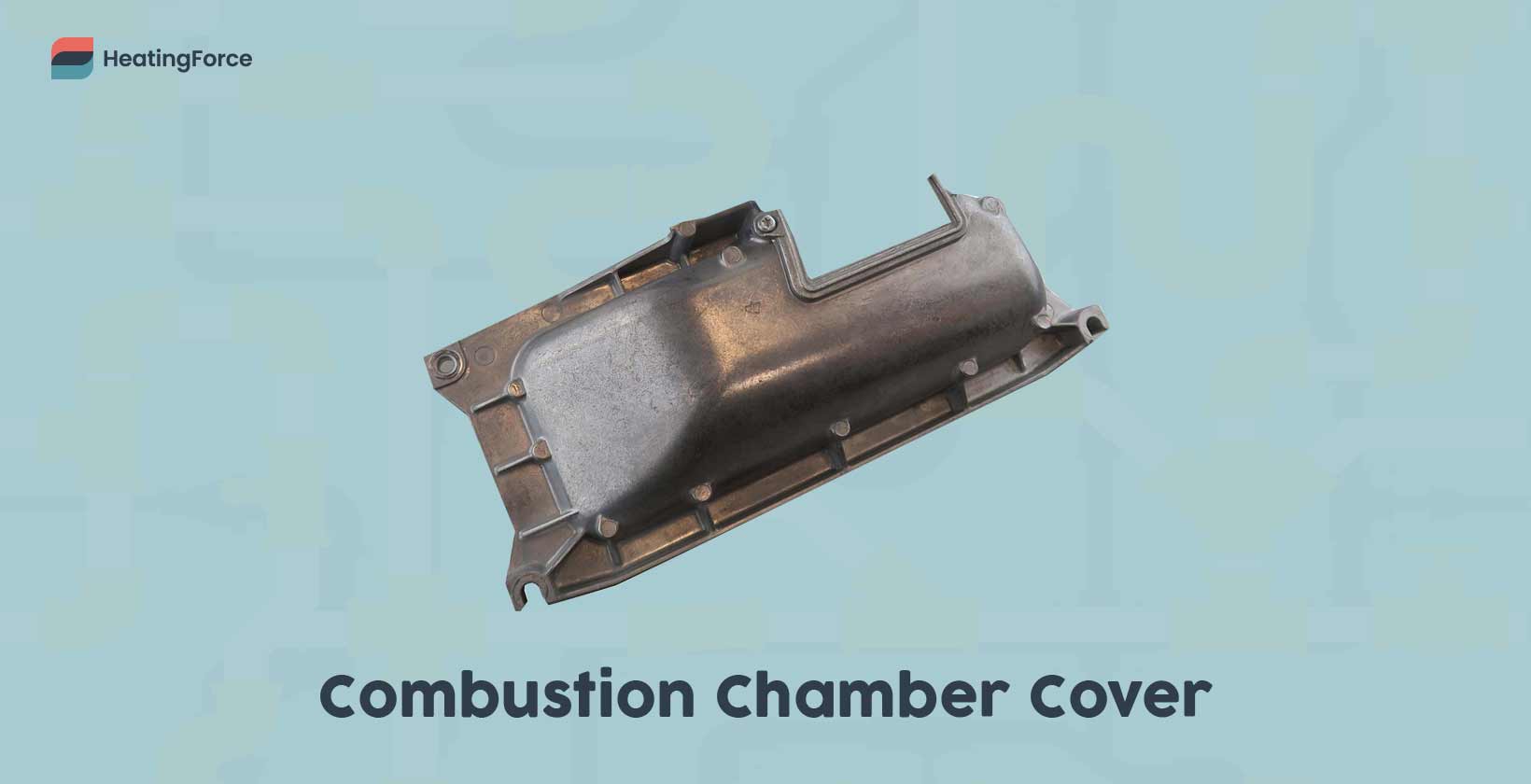
The combustion chamber is an enclosure in which fuel ignites to produce heat. It’s designed to ensure efficient and safe burning of the gas.
A well-maintained combustion chamber ensures complete and efficient ignition of the fuel, thus reducing waste and harmful emissions. Regular inspection and maintenance of the part are thus vital and must involve checks for signs of damage, corrosion, or carbon buildup. The presence of any of the issues above impedes the boiler’s performance and safety.
The cost of replacing a combustion chamber varies depending on the boiler’s make and model. However, getting all of the components necessary to replace a boiler’s combustion chamber assembly costs between £150-£200, not accounting for labour. Finding combustion chamber components is generally a challenge, as they are not widely stocked.
4. Refractory
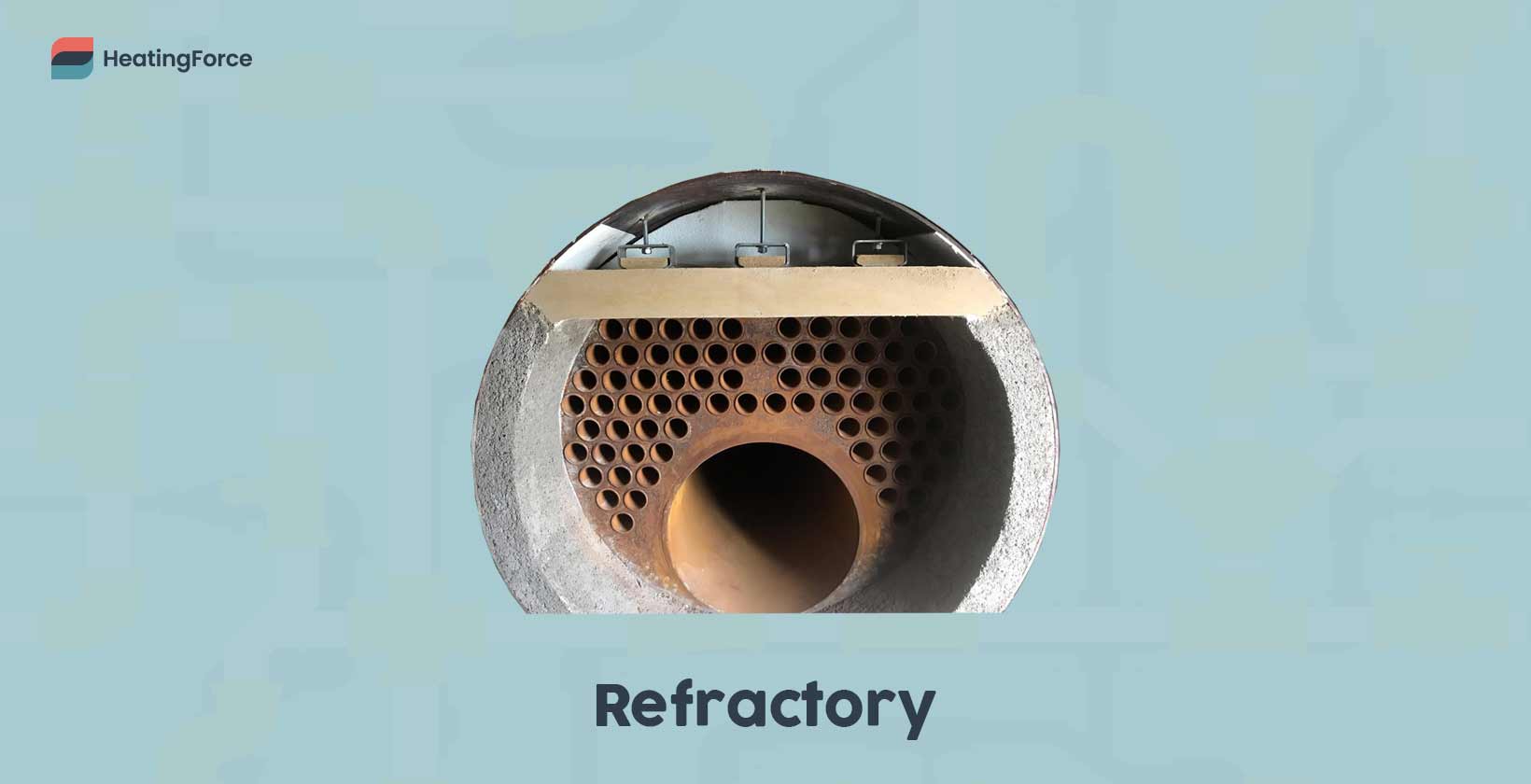
The refractory acts as a heat-resistant lining for the combustion chamber in a boiler. The part helps contain the intense heat generated during the combustion process, ensuring it transfers efficiently to the water in the boiler. Refractories are common in large, industrial boilers but not in domestic ones, where the combustion chamber serves a similar purpose.
5. Ignition system
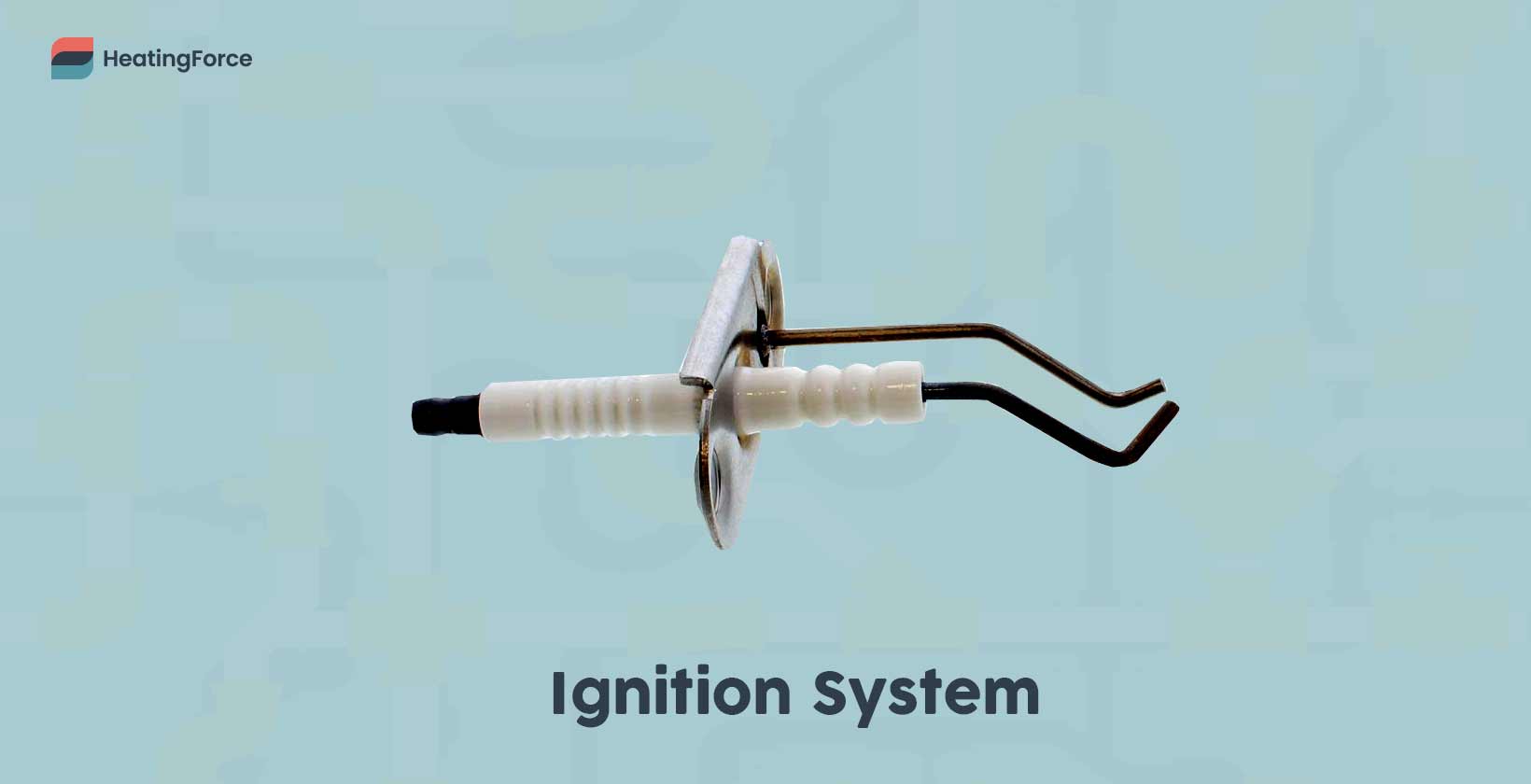
A boiler’s ignition system initiates the combustion process. The system typically includes an igniter and a flame sensor, which work together to ensure a safe and efficient start-up of the boiler.
Gas boiler ignition systems use an electric spark or a hot surface igniter to ignite the gas-air mixture. The flame sensor confirms the presence of a flame after ignition, allowing the boiler to continue operating. If no flame is detected, the system shuts down to prevent unburned gas from accumulating and creating a safety hazard. The ignition process in oil boilers involves heating oil to its ignition point and producing an electric spark to start the burner. Safety mechanisms similar to those in gas boilers are in place to detect and prevent issues in their oil-fired counterparts.
The reliability and efficiency of the ignition system are key to the overall performance of the boiler. Over time, components of the ignition system may wear out or become dirty, and stop functioning properly as a result. A faulty ignition system may lead to issues such as intermittent heating or failure to start. Regular maintenance, including checks and cleaning of the igniter and flame sensor, is important to maintain the boiler’s optimal performance.
The cost of a new boiler ignition unit ranges between £100 and £150, not accounting for labour. Ignition systems for most modern boilers are easy to find at online and physical heating and plumbing supply stores across the UK.
6. Pilot light
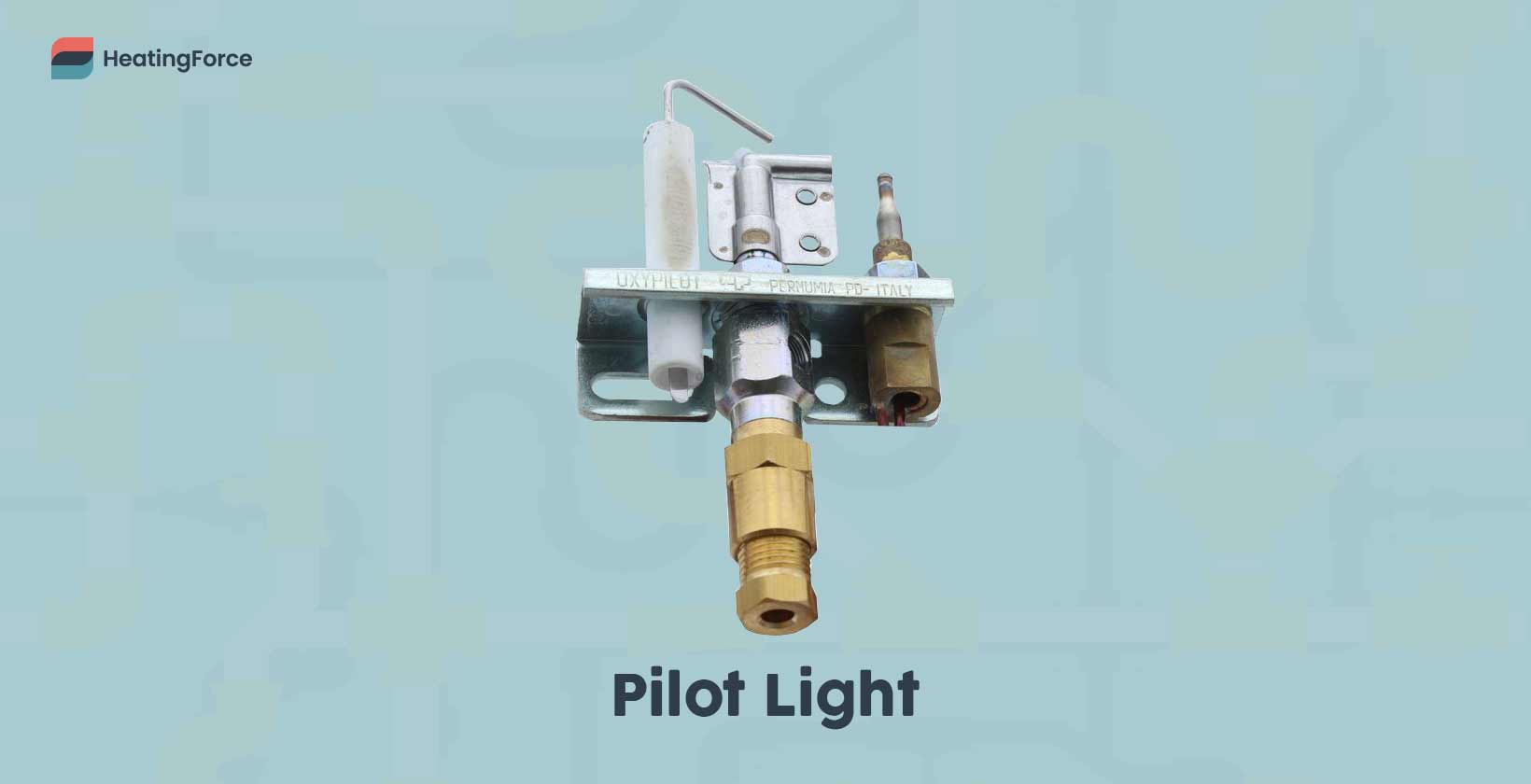
The pilot light is a small, continuously burning flame used to ignite the main burner when the boiler is turned on. These components are more commonly found in older gas boilers, as many modern boilers use electronic ignition systems instead. The component provides a reliable and immediate source of ignition but means that a small amount of gas is continuously burned even when the boiler is not heating.
Regular checks are necessary to confirm that the pilot light is clear of debris and functioning as intended. If the pilot light frequently goes out or struggles to stay lit, it may impede the boiler’s function and requires prompt professional attention.
Replacing a pilot light is not an expensive affair, as the part seldom costs more than £60 without labour. However, pilot lights are usually present in older boiler models, and as such they are not always widely available.
7. Expansion tank
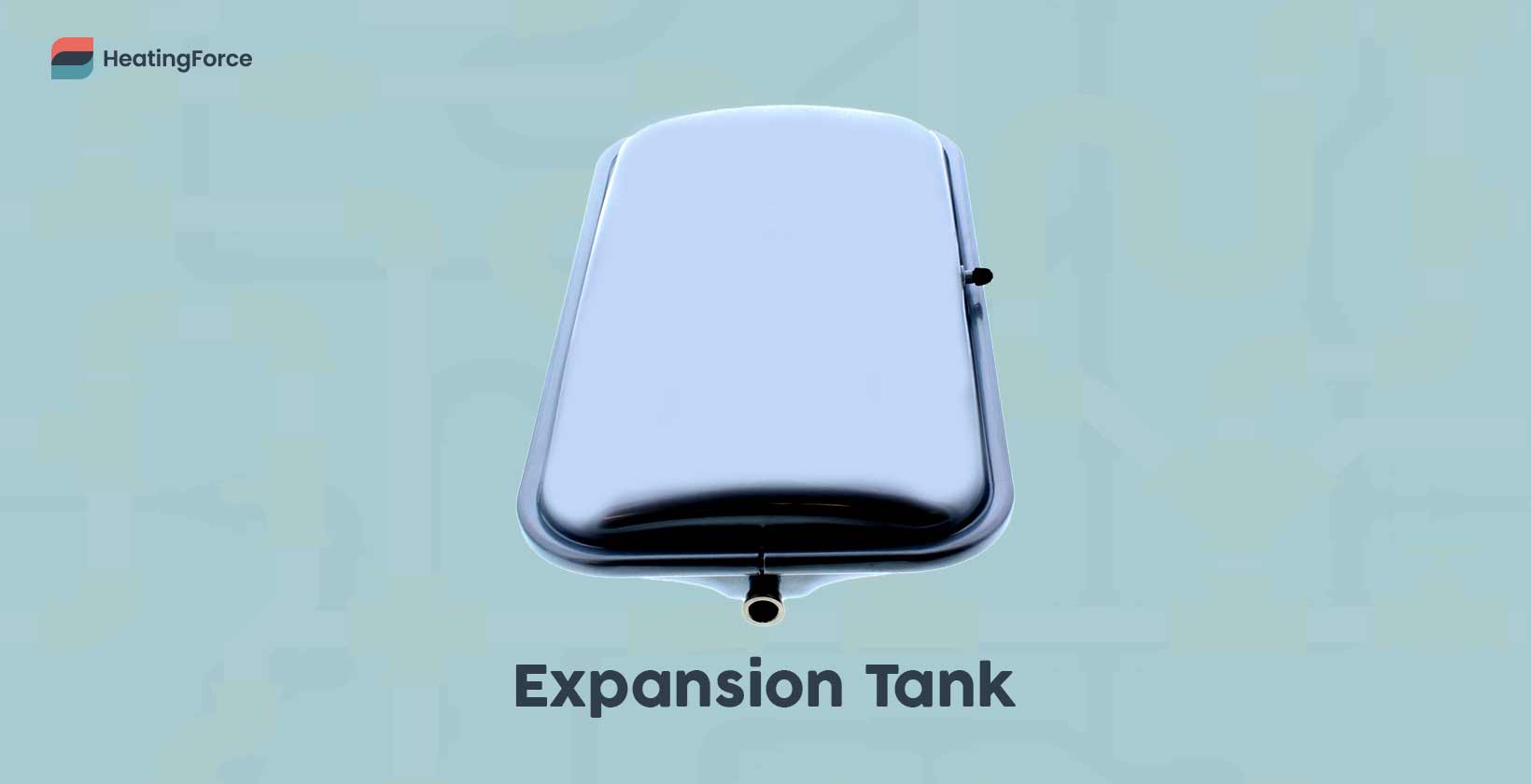
The expansion tank (also known as the “expansion vessel”) is a vital boiler component designed to accommodate the expansion of water as it heats up. It helps to maintain consistent pressure within the boiler system, thus preventing potential issues like leaks or pressure build-up. Combi and system boilers generally have an integral expansion tank, whilst the open-vented regular boilers rely on an external feed-and-expansion tank to handle water volume changes.
Age-related wear and tear may cause the expansion tank to develop faults and leak water. Routine annual checks are thus necessary to ensure that the expansion tank functions correctly and maintains the right pressure level in the heating system. However, an expansion vessel that’s damaged beyond repair and is letting by water requires prompt replacement. The price of a brand-new expansion vessel hovers around £300, not accounting for installation costs. Since the majority of modern combi and system boilers have an integral expansion vessel, finding a spare is seldom an issue in the UK. The only instance in which you may struggle to source a new expansion tank is if your boiler model is obsolete.
8. Controls
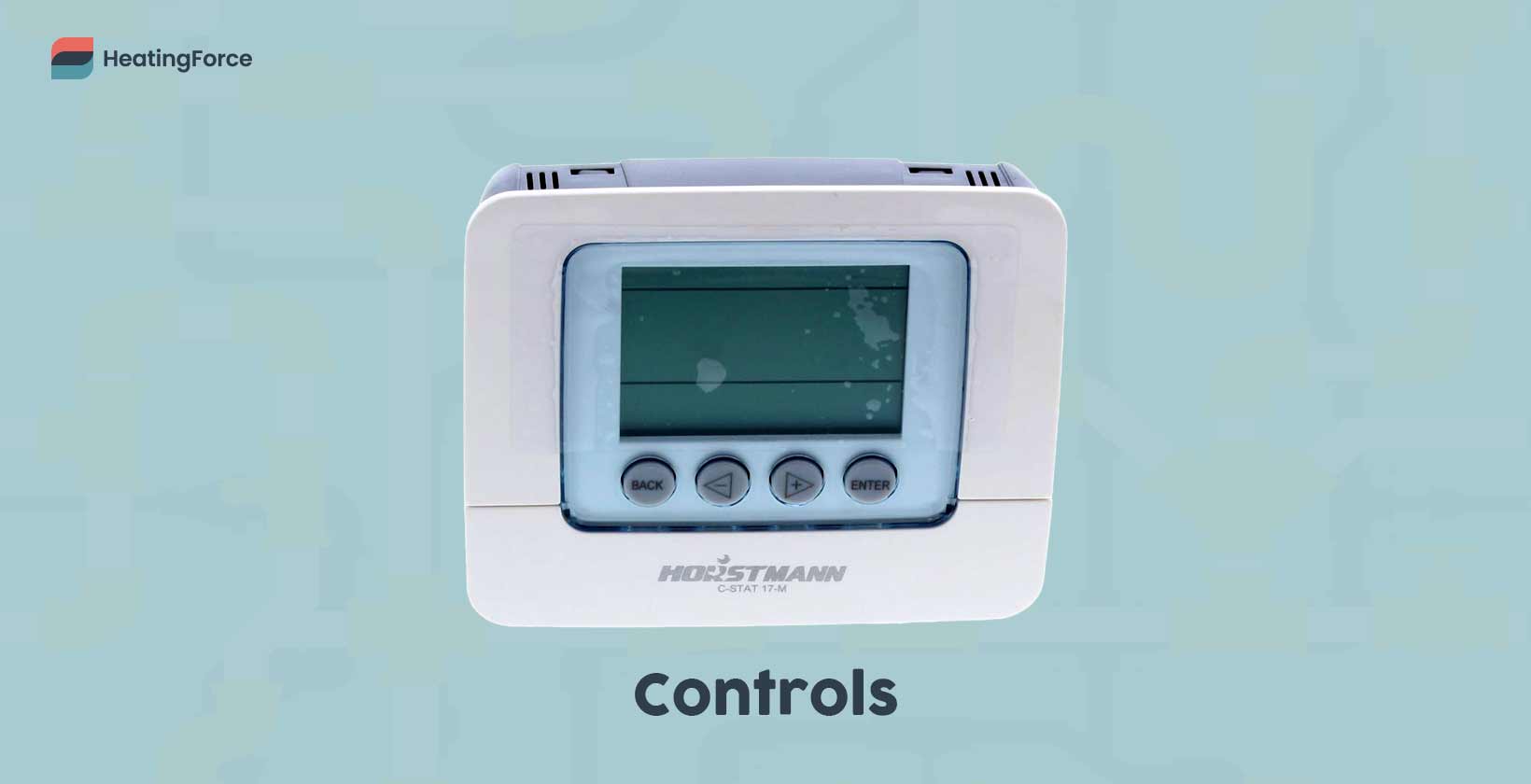
Boiler controls allow users to set the desired temperature, manage the heating programme, and control specific heating zones within the home. These controls range from basic thermostats to advanced programmable systems that offer greater flexibility and efficiency.
Servicing boiler controls is important for the consistent and safe operation of the boiler. Their maintenance involves ensuring correct calibration and testing their ability to relay boiler commands. Regular software updates to the boiler controls additionally contribute to a more efficient, user-friendly heating system.
The cost of a boiler control system ranges depending on its manufacturer and level of sophistication. Smart or programmable thermostats from brands such as Google Nest, tado°, or Hive may cost anywhere between £100-£350 before installation. Meanwhile, a new “dumb” digital controller ranges between £40-£80. A wide assortment of boiler controls is available in online and physical shops across the UK.
9. Timer
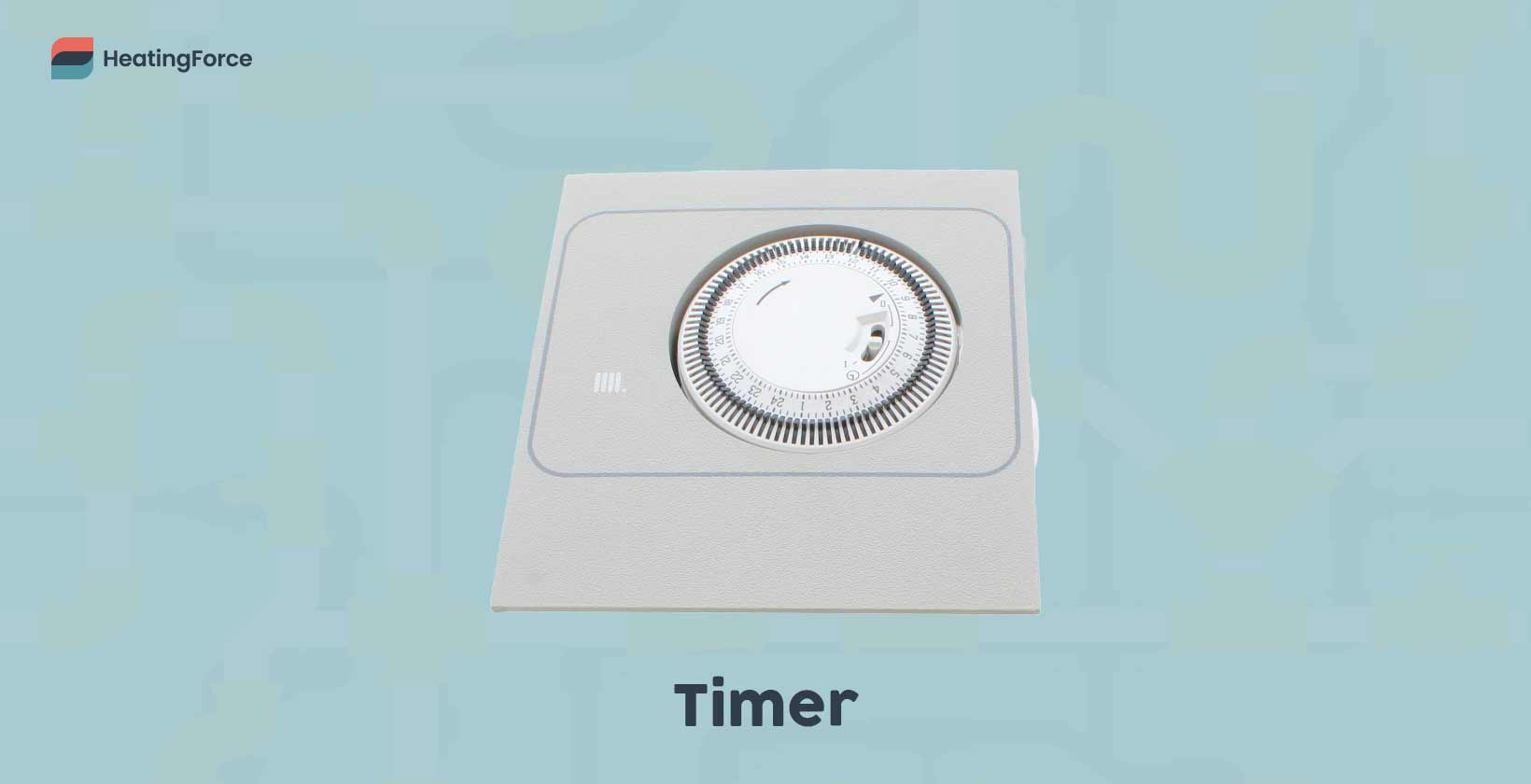
The timer in a boiler is a rudimentary, integral control mechanism that allows homeowners to control when the heating system turns on and off. Setting the boiler to operate only at specific times allows users to heat their homes only when needed, thus avoiding unnecessary energy consumption.
Timers range from simple analogue devices to sophisticated digital controls. They offer flexibility in heating schedules that enable daily or weekly programming to match the household’s routine. Advanced timers even allow different settings for weekdays and weekends.
Regular checks of the timer’s functionality ensure it remains accurate and reliable, and the servicing technician typically performs these checks during annual boiler service. A broken boiler timer is generally easy to replace, as brand-new parts from various models are widely available nationwide. The prices for new boiler timers span between £40-£100, not including labour costs.
10. Printed Circuit Board (PCB)
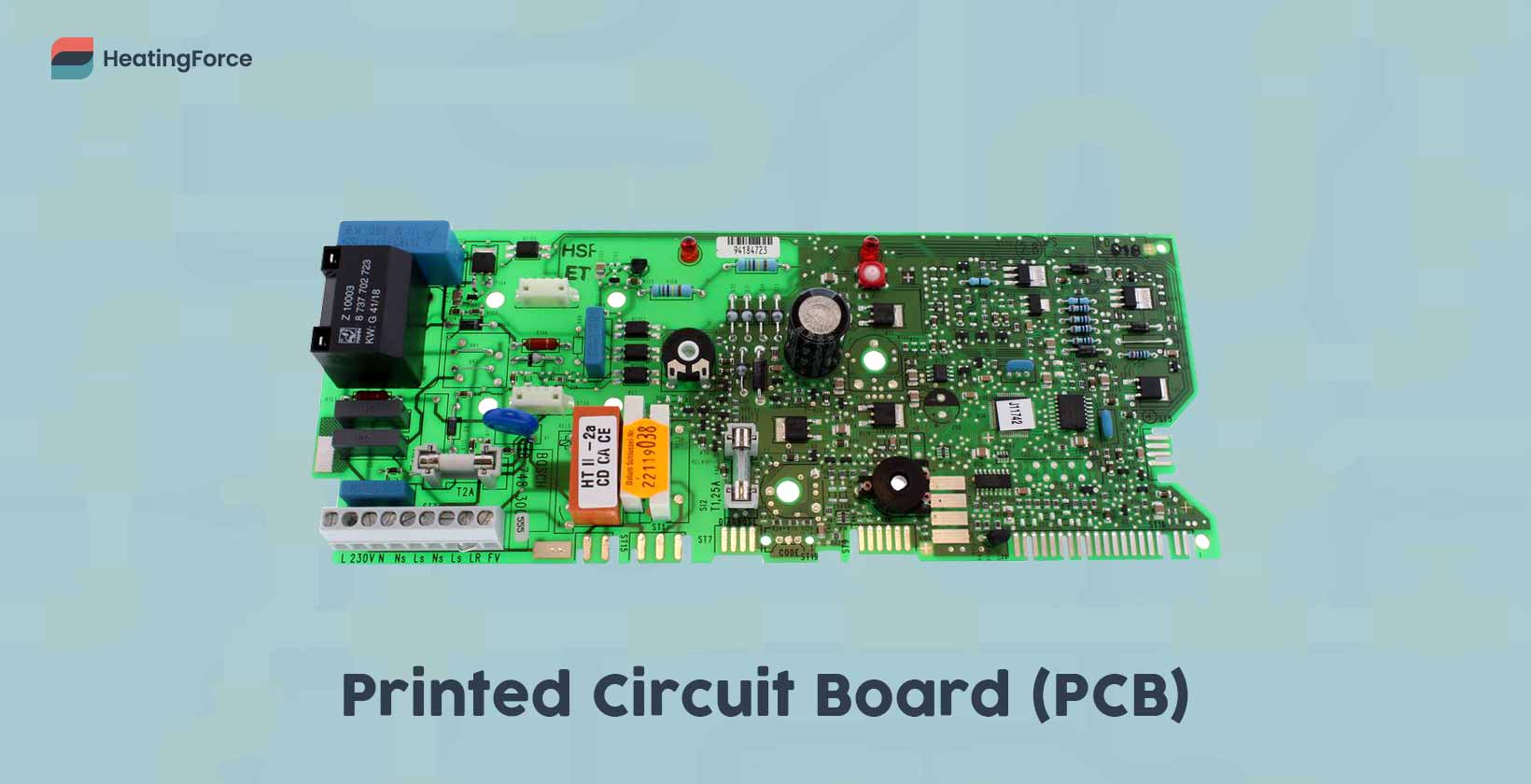
The printed circuit board (PCB) is a key electronic component that controls and manages the boiler’s various functions. It’s essentially the boiler’s “brain,” as it relays commands between different components and ensures that the system operates efficiently and safely. This PCB manages tasks such as ignition, temperature monitoring, burner regulation, and circulator pump controls. It additionally plays a role in diagnosing issues, as many modern PCBs generate error codes that help identify specific problems.
Routine servicing by qualified professionals helps identify potential issues with the PCB before they lead to major problems. The complexity and importance of the PCB make it one of the most expensive boiler components, with average replacement costs ranging between £350 and £500 without labour. You should have no trouble finding a new PCB in the UK if you have a modern boiler from a well-known brand.
11. Aquastats
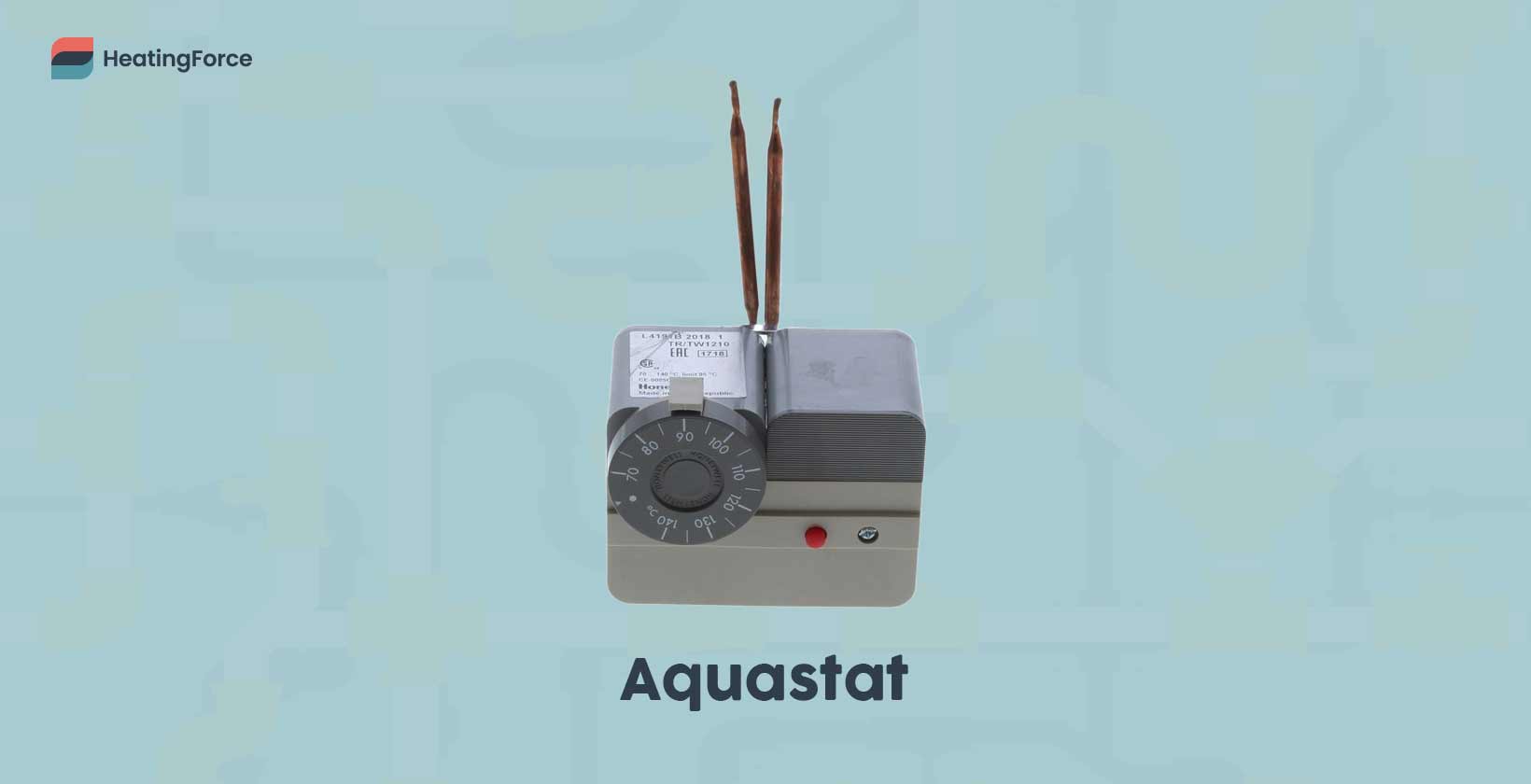
Boiler aquastats are devices that regulate the domestic hot water temperature. The device monitors the water temperature in the hot water cylinder and adjusts the burner’s operation to maintain the desired temperature range. Heating systems powered by regular and system boilers generally contain an aquastat, whilst those powered by combis do not.
Below are the two different types of aquastats.
- High-limit aquastat: The high-limit aquastat prevents the water from overheating, as excessive water temperatures are unsafe and inefficient.
- Low-limit aquastat: The low-limit aquastat ensures the water temperature doesn’t drop below a certain point. Keeping the water temperature above 60ºC prevents the deadly Legionella bacteria from contaminating the home’s drinking water.
Frequent servicing of aquastats is essential for the efficient and safe operation of the boiler. A malfunctioning aquastat may lead to issues such as water overheating or being insufficiently hot, thus leading to possible Legionella growth in the hot water cylinder.
Replacing an irreparable aquastat costs between £60-£100 without labour, depending on the hot water cylinder make and model. Replacement aquastats are generally available at plumbing and heating supply stores, as well as online from manufacturers of hot water cylinders.
12. Overheat thermostat
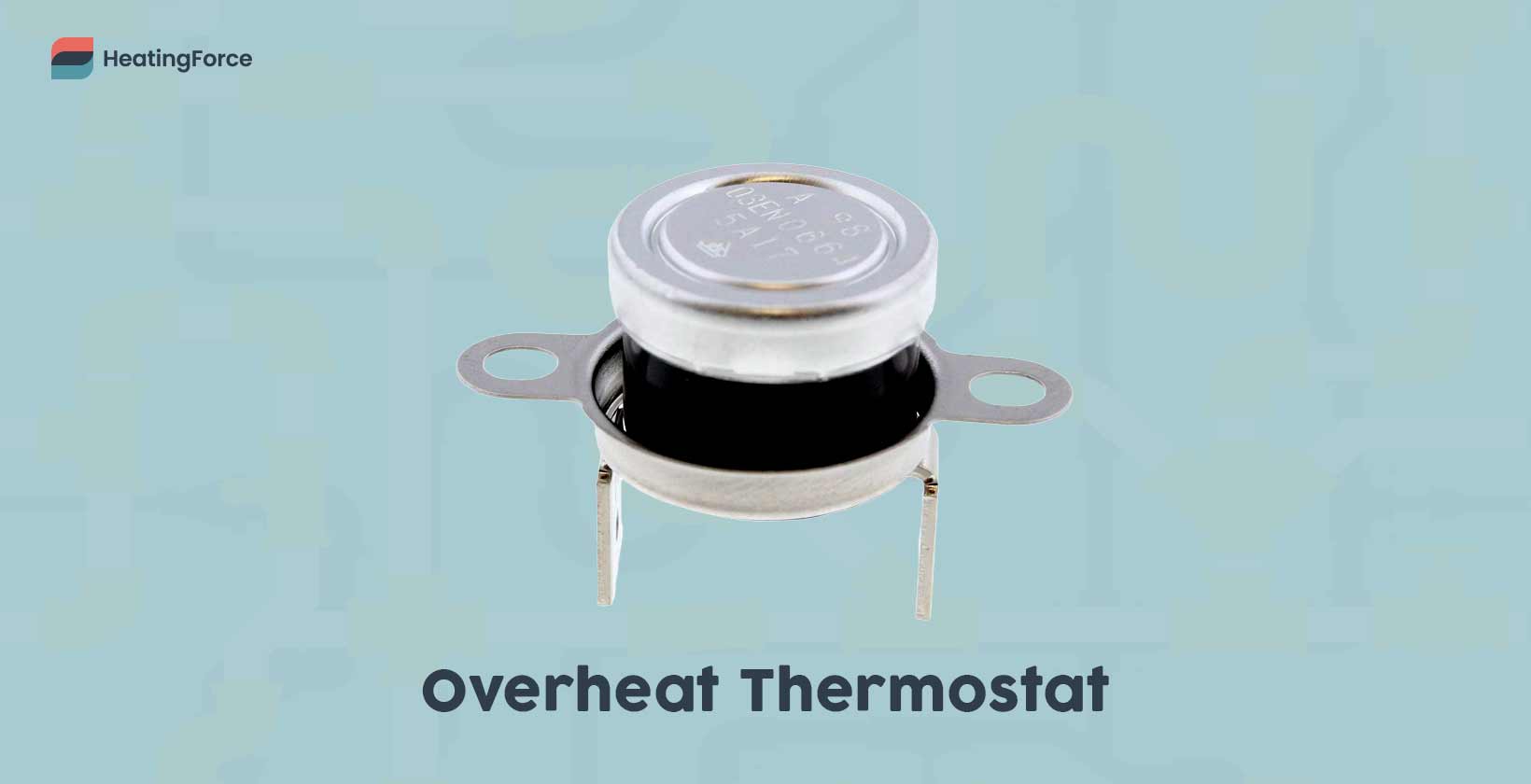
The overheat thermostat is a critical safety feature designed to prevent the boiler from overheating. Excessively high water temperature causes the boiler pressure to increase beyond normal operating levels and puts undue strain on the internal components. The thermostat works by monitoring the temperature within the boiler and shutting off the fuel supply if the internal temperature exceeds a safe limit.
Regular boiler servicing should include checks of the overheat thermostat. Verifying that the thermostat is responsive and accurate is crucial because malfunctions of this component may pose risks to the boiler and the household.
The cost of a new overheat thermostat is relatively small, with part-only prices ranging from £15 to £60, depending on the model. Finding a new overheat thermostat normally isn’t a challenge unless the boiler model is obsolete.
13. Superheater
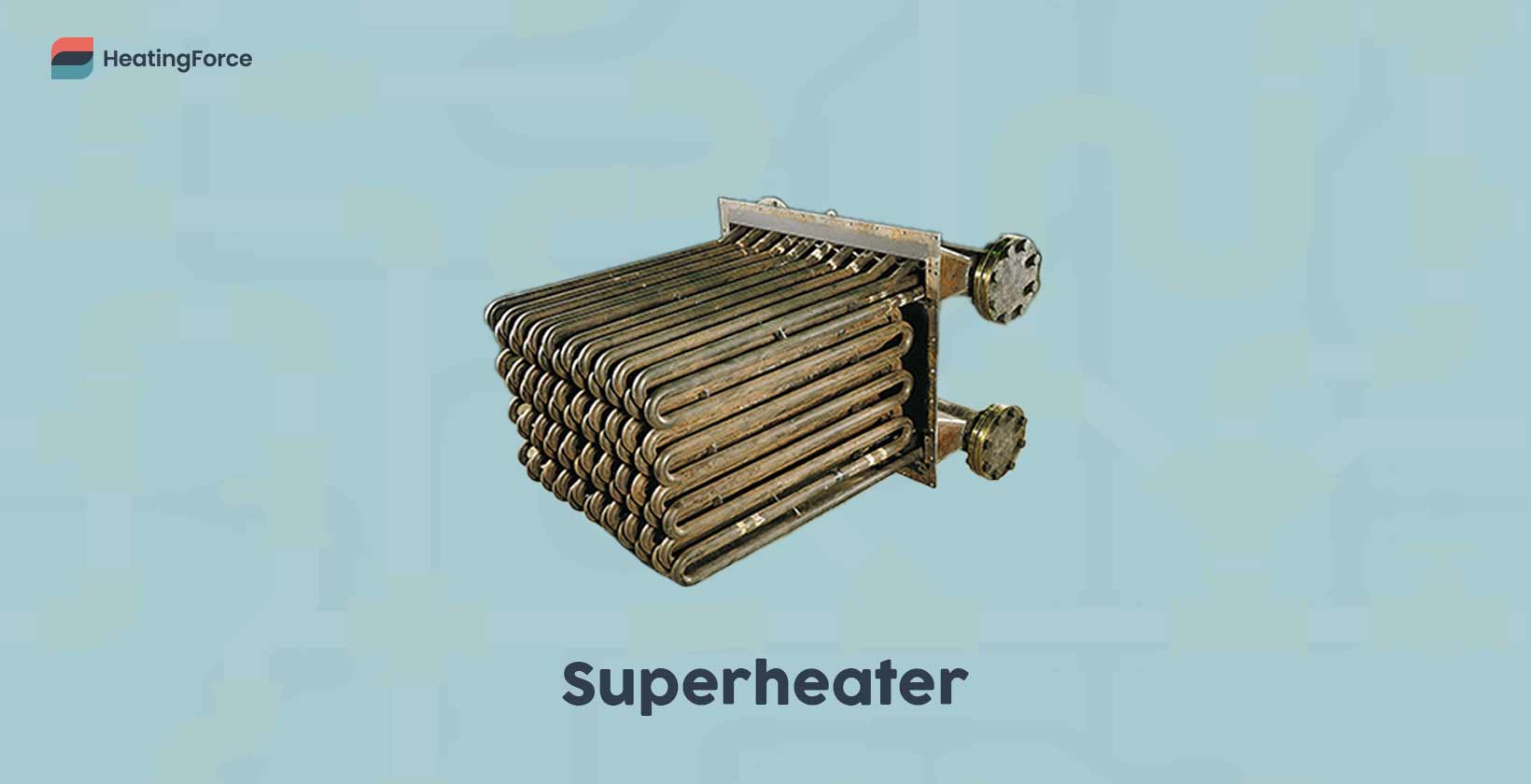
A superheater is a boiler component that increases the temperature of steam beyond its saturation point without raising its pressure. The superheating process is particularly useful in power generation and heavy industrial applications where superheated steam is required for efficient operation.
Superheaters are common in large-scale industrial or commercial boilers, but not in residential gas boilers. In residential heating, a boiler’s focus is on heating water for domestic use or central heating, and it does not produce steam in the first place.
14. Circulator pump
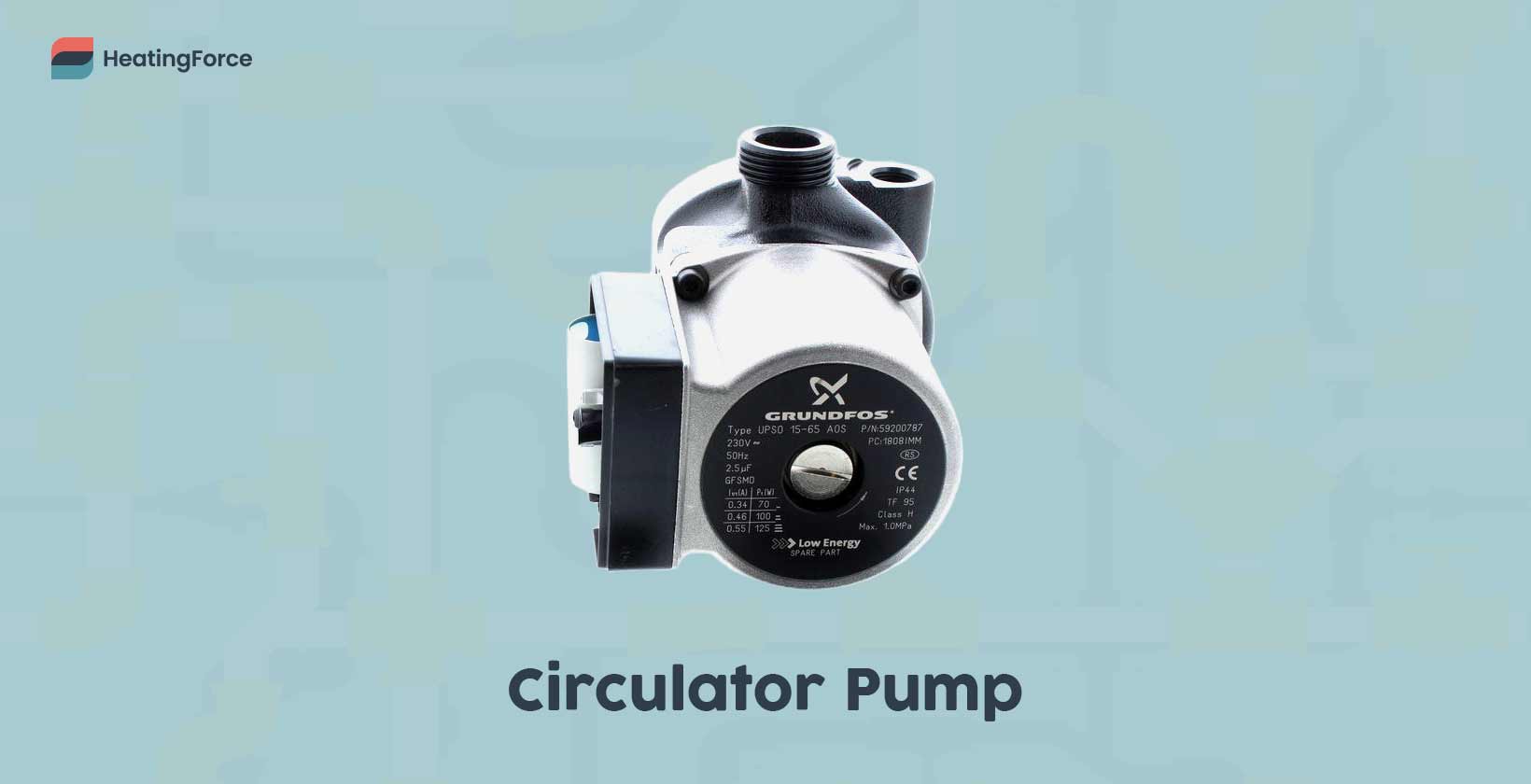
The circulator pump is a boiler component that ensures the circulation of hot water throughout the heating system. Combi and system boilers typically have an integral circulator pump, whilst conventional boilers work with an external pump that’s connected to the heating pipework. Regardless of the boiler type, the pump’s operation is generally quiet and its speed is adjustable to suit the specific heating needs of the household.
Annual servicing of the circulator pump is important for the longevity and efficiency of the boiler and central heating system. During boiler service, the Gas Safe (or OFTEC) registered engineer must check the pump for leaks and signs of wear and tear. Minor flaws, such as blown seals or worn-out gaskets entail a simple fix. Meanwhile, severe damage to the pump typically necessitates a replacement, which costs between £150-£200. Circulator pumps from various manufacturers (such as Grundfos and Wilo) are readily available, but you must make sure the replacement is compatible with the boiler model.
15. Economiser
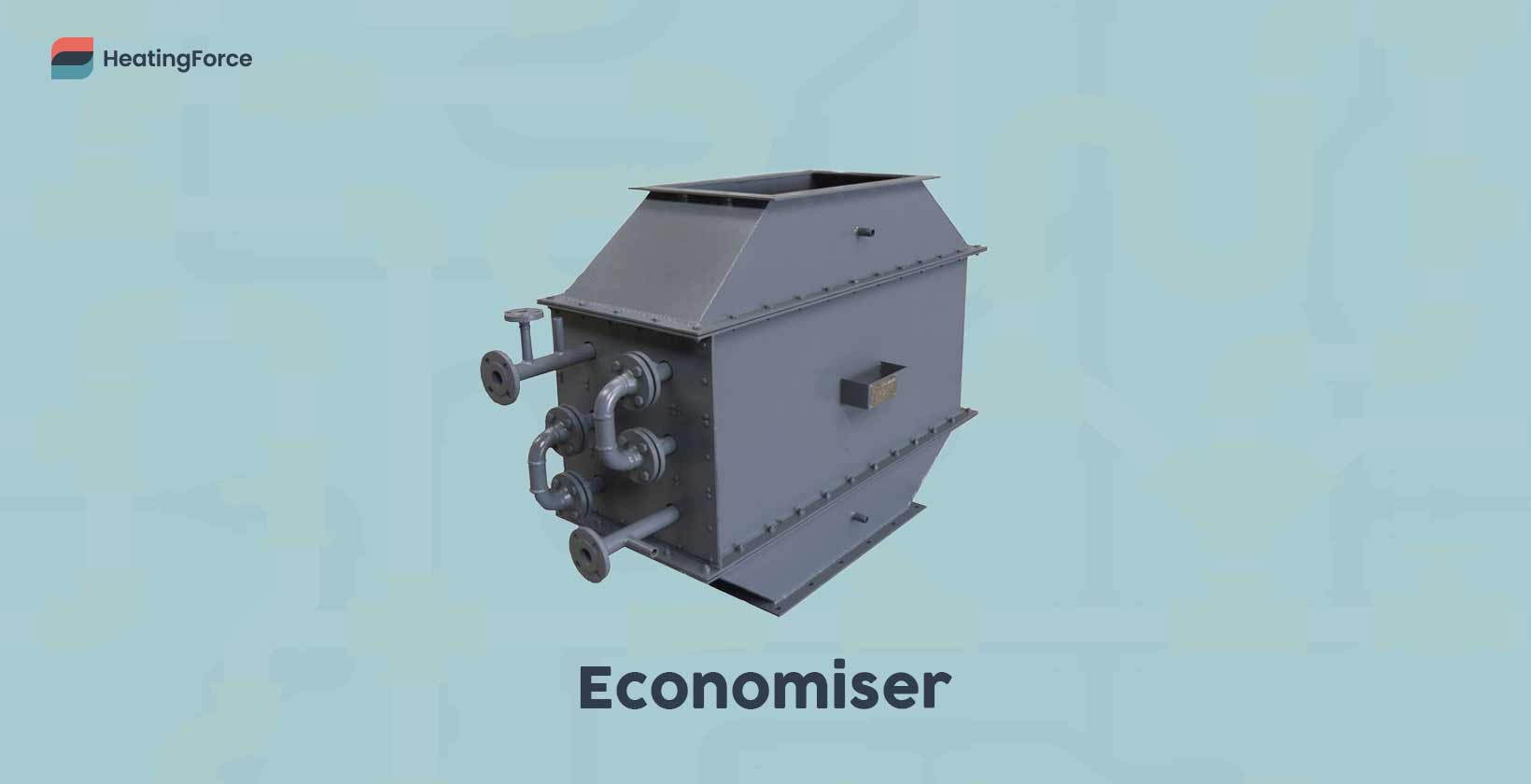
An economiser is a component that recovers heat from the boiler’s exhaust gases, and then uses it to preheat the boiler feedwater. This recovery process improves boiler efficiency by reducing the amount of energy required to heat the water to the desired temperature.
Residential boilers do not come with an economiser. Instead, condensing domestic boilers rely on their heat exchangers to recapture the latent heat in exhaust fumes.
16. Backflow valve
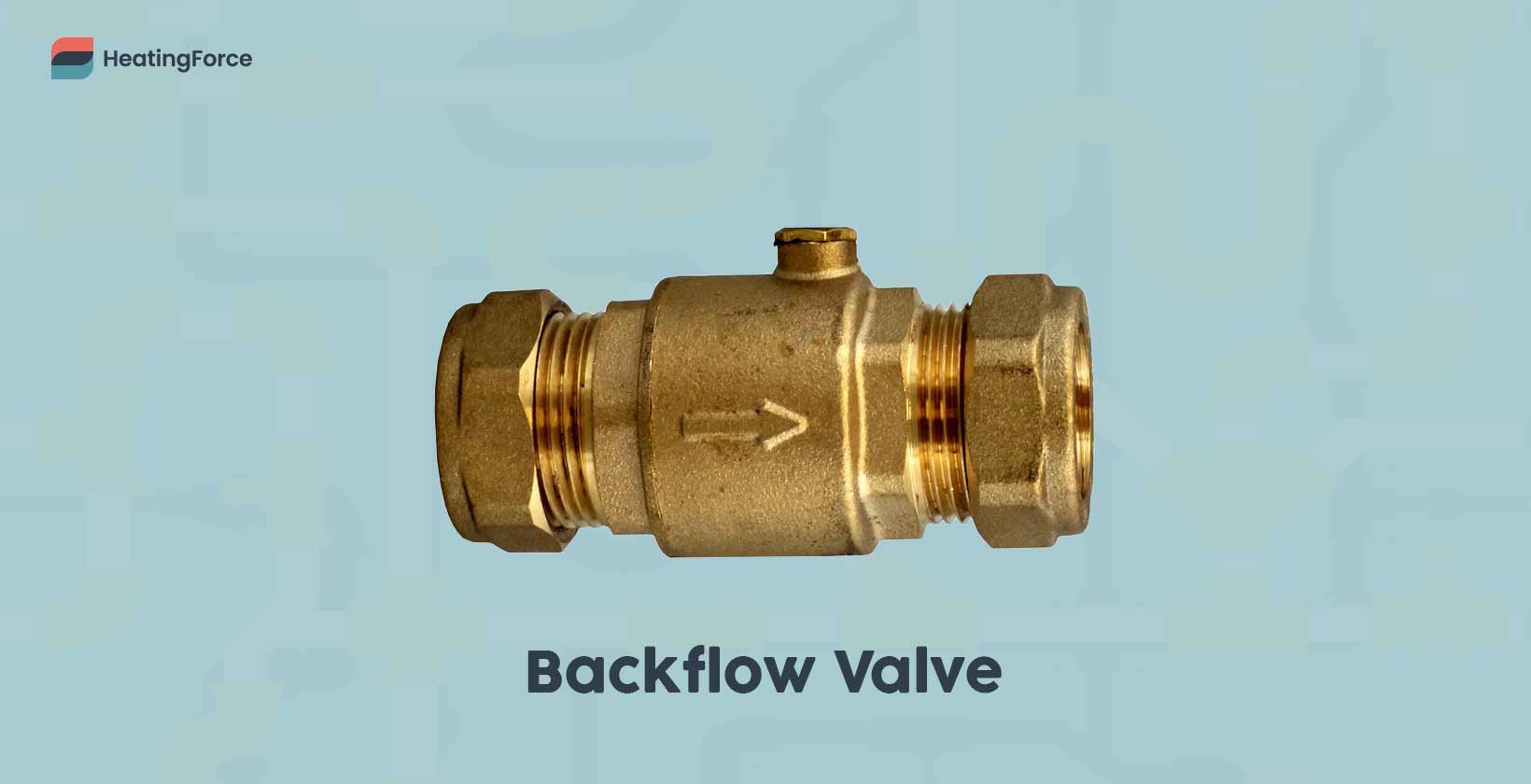
The backflow valve (also known as a “check valve” or “backflow preventer”) is a safety component that prevents the reverse flow of water within the heating system. The valve thus ensures that the home’s heating water does not mix with the cold water supply. This precaution maintains the quality of the domestic hot water, as it averts the possibility of it becoming contaminated with dirty heating water.
Routine checks of the backflow valve are essential during annual boiler service. Any malfunction or failure of this valve may lead to water contamination or system inefficiency. The cost of replacing an irreparable backflow valve is between £50 and £100 without installation, depending on the boiler brand and model. You should have no issues with sourcing a new check valve either online or at a brick-and-mortar supply store.
17. Pressure Release Valve (PRV)
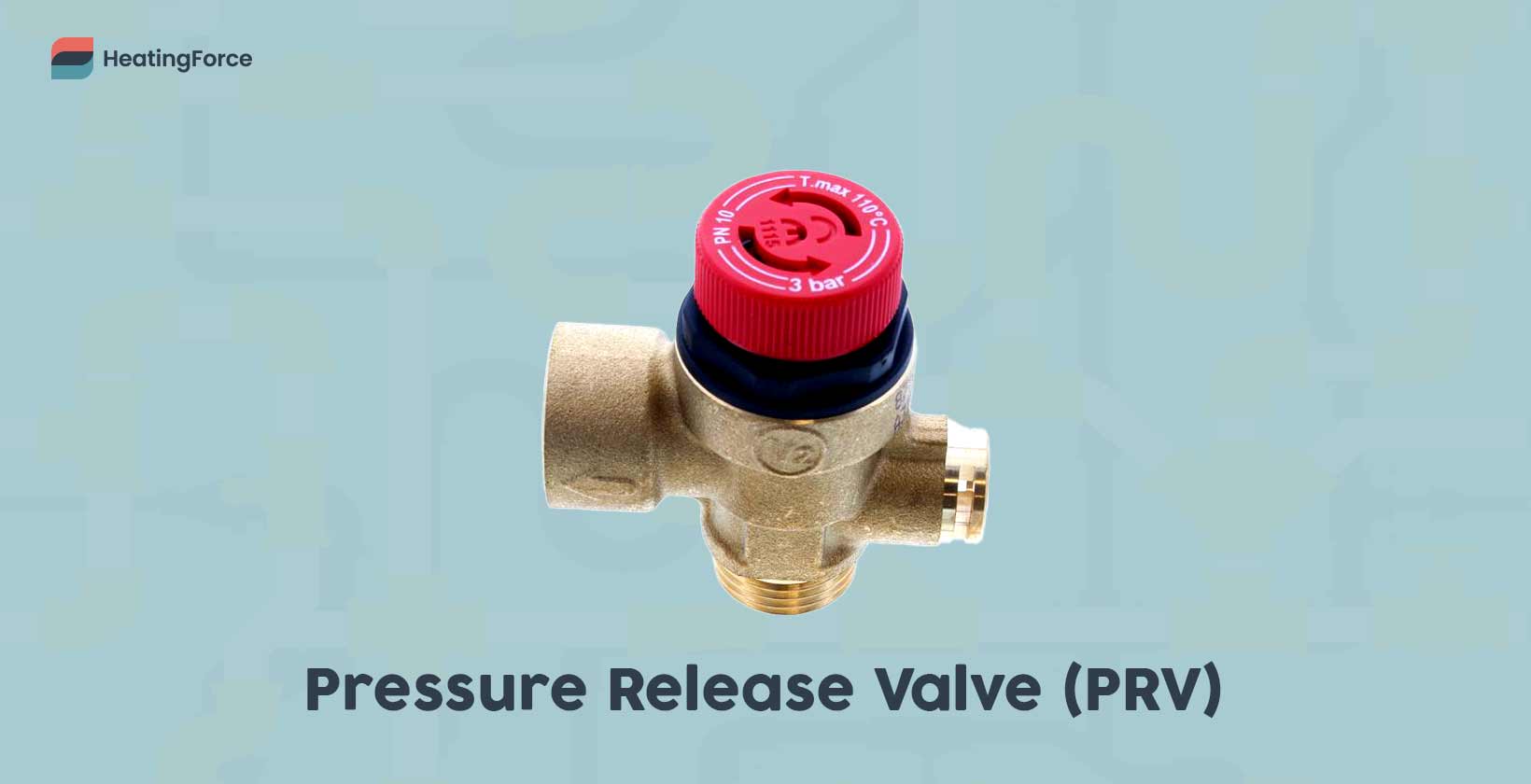
The Pressure Release Valve (PRV) is an essential boiler safety feature. It automatically releases water if the boiler pressure reaches an excessively high level and protects the boiler components from undue stress.
A faulty PRV may cause the boiler pressure to drop by leaking water, or fail to release pressure once it’s climbed over the safe operating threshold. Routine checks of the PRV are therefore important in ensuring that the boiler and heating system function properly. The technician performing annual boiler service should generally check and confirm that the PRV works as it should. Fixing insignificant PRV faults is typically inexpensive. However, even replacing a heavily damaged valve doesn’t cost much either: prices for brand-new PRVs vary between £15-£50, without installation. Most plumbing and heating supply shops have various boiler PRV models on hand.
18. Diverter valve
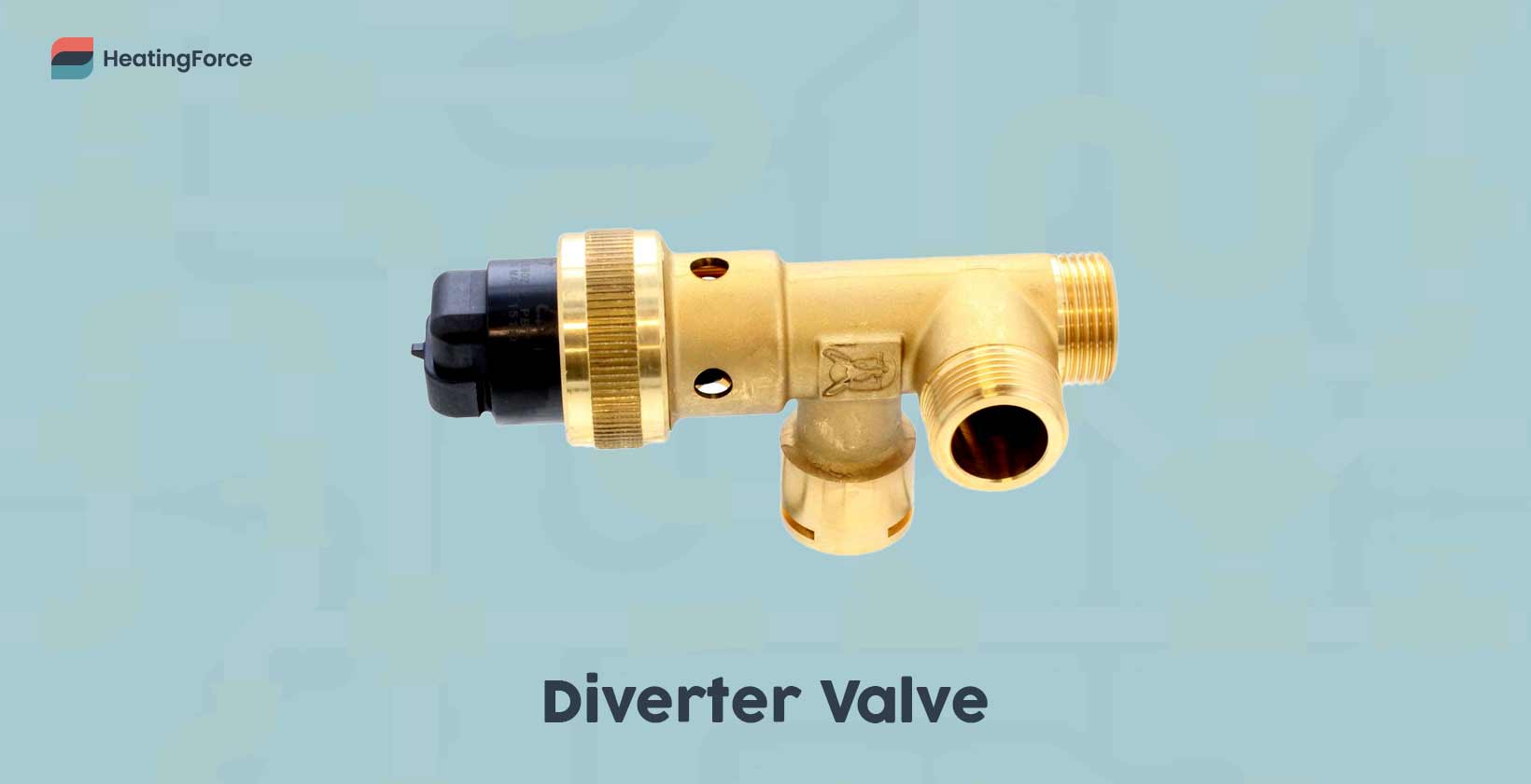
The diverter valve is a component that directs the flow of hot water either to the radiators for heating or to the taps for domestic hot water use. This valve plays a crucial role in combi boilers, where both heating and hot water are provided by the same unit. When a hot water tap is turned on, the diverter valve temporarily redirects hot water away from the heating system to the taps. Once the tap is turned off, the valve switches back, resuming hot water flow to the radiators. System and regular boilers do not have an integral diverter valve, since they only generate water for the central heating system.
Checking the diverter valve during annual boiler service is crucial to ensure it operates smoothly. Issues with the diverter valve lead to problems such as hot water not reaching the taps or the radiators not heating up. Faulty diverter valves often require a simple fix or clean-up, but severe damage due to age and wear and tear may warrant a replacement of the part. Brand-new diverter valves cost in the region of £350-£450, not accounting for labour and are readily accessible at physical and only boiler part shops.
19. Auto-air vent
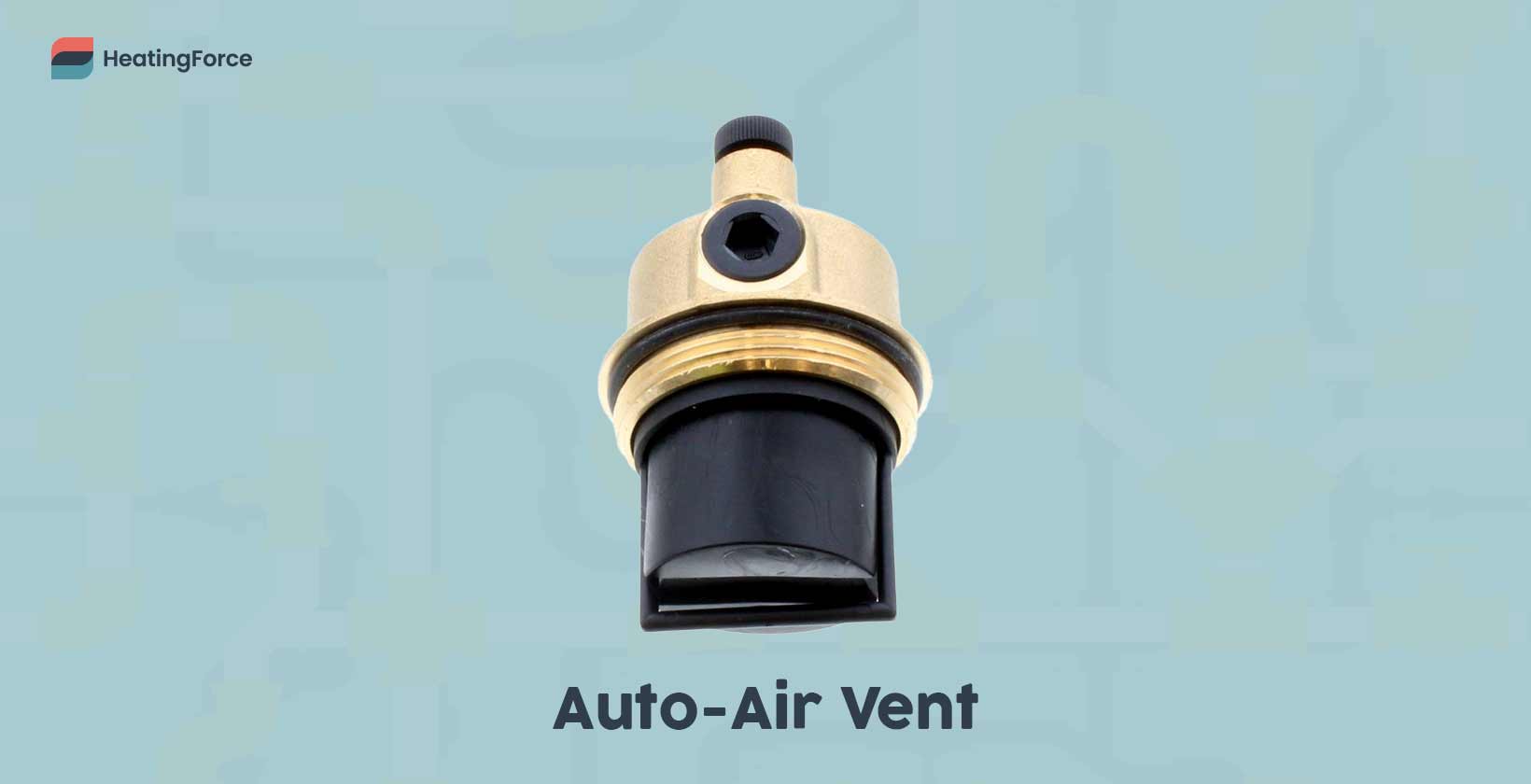
An auto-air vent is a boiler component that releases trapped air from the heating system. Trapped air in a boiler leads to inefficiencies such as increased noise, uneven heating, and poor water circulation in the heating system. The auto-air vent is strategically located at the highest point where air is likely to accumulate.
Inspecting the auto-air vent during annual boiler service ensures that no flaws are preventing it from letting out trapped air. The servicing technician may be able to rectify minor flaws with an air vent at a minimal cost. However, worn-out air vents that are beyond repair must be replaced, and the cost of a brand-new vent is upwards of £170, excluding labour. Procuring a new auto-air vent is easy both at online and brick-and-mortar boiler spare shops.
20. Fan
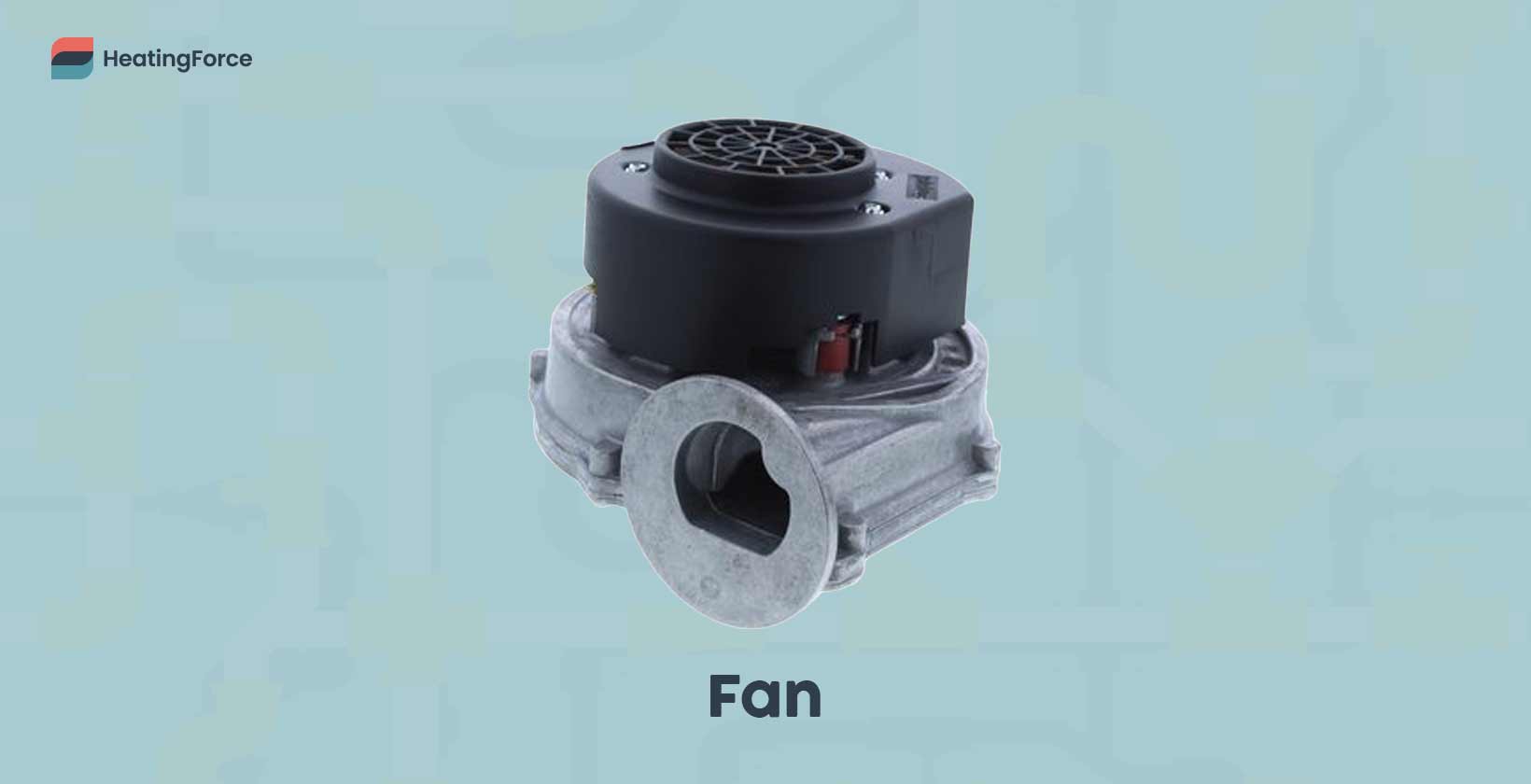
The fan is a safety component that draws exhaust gases from the boiler’s burner and pushes them through to the outdoors through the flue. It additionally prevents moist exhaust gases from accumulating around the heat exchanger and producing excessive amounts of condensate, which may corrode the boiler’s internal parts. Contrary to popular belief, the boiler’s fan does not cool the boiler down – the water circulating in and out of the boiler cools it naturally while picking up the heat it generates.
Fans require annual checkups along with boiler service, as such inspections help detect and rectify issues with the part before they progress. A faulty boiler fan may be unable to expel toxic exhaust fumes from the combustion chamber. When the fan fails to generate sufficient air pressure in the exhaust stack, the boiler’s air pressure switch detects the low pressure and shuts the boiler down as a precaution. This safety process prevents lethal carbon monoxide from building up inside the home.
Replacing a malfunctioning boiler fan is not a minor expense, as new fans cost between £200-£300 depending on the boiler brand and model. You’re able to source the fan from a boiler spares shop, either online or at a physical location.
21. Exhaust stack (flue)
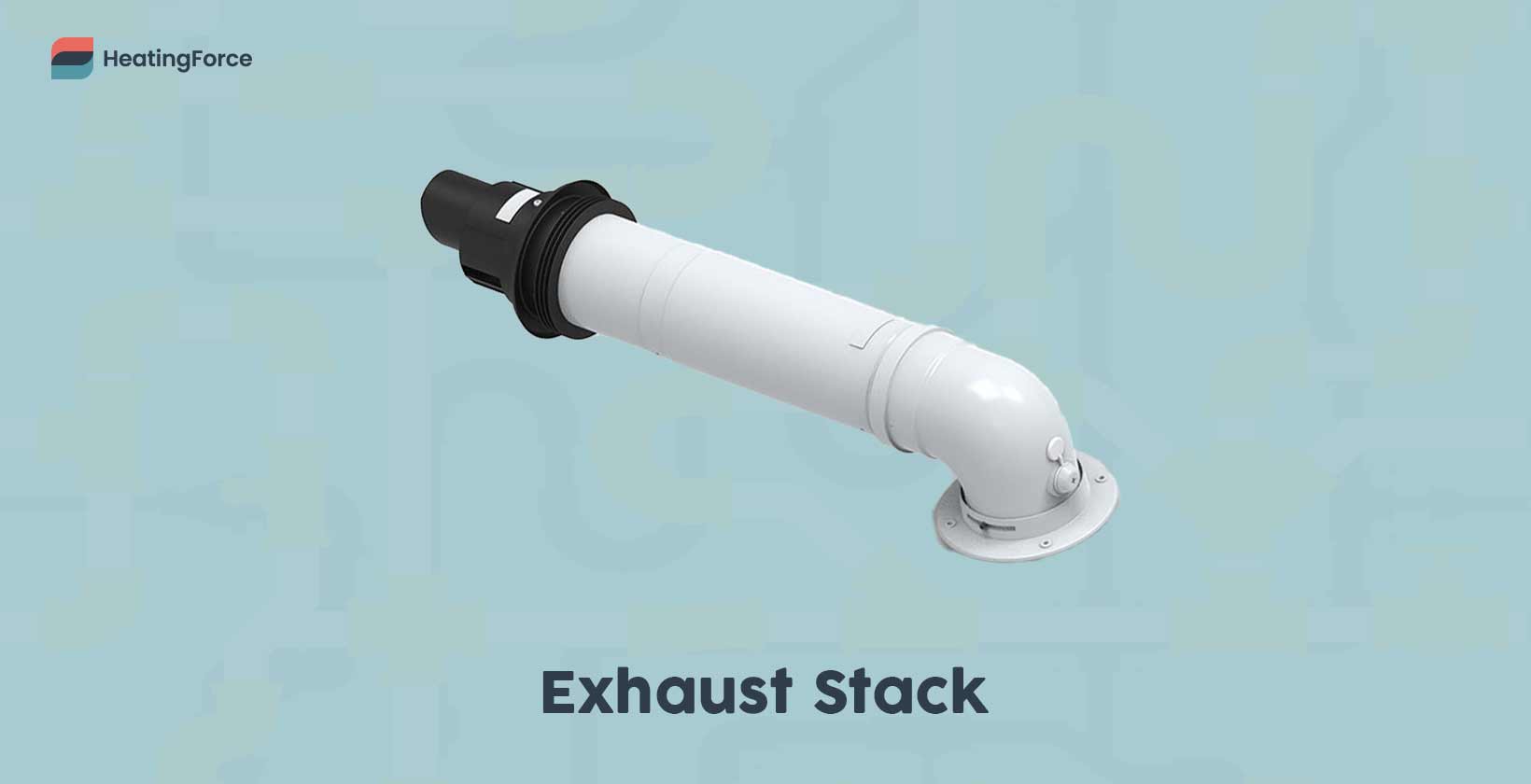
The exhaust stack (commonly known as the “flue”) is a pipe that channels combustion gases away from the boiler and out of the home. It ensures that carbon monoxide and other harmful fumes vent safely outside. Flues in modern boilers are designed to withstand high temperatures and corrosive gases.
Regular inspection and maintenance of the flue are critical. Debris such as leaves and bird feathers may block the flue, leading to boiler lockouts. Meanwhile, cracks in the flue may lead to the accumulation of toxic fumes inside the home. To prevent the aforementioned issues, the boiler’s exhaust stack must undergo a thorough inspection during the annual boiler service. Heavily damaged exhaust stacks require prompt replacement, with new flue kits costing anywhere between £150 and £1,000 depending on the boiler make, model, and flue configuration. Most boiler manufacturers sell replacement flue kits, as do heating and plumbing merchants.
22. Gas valve
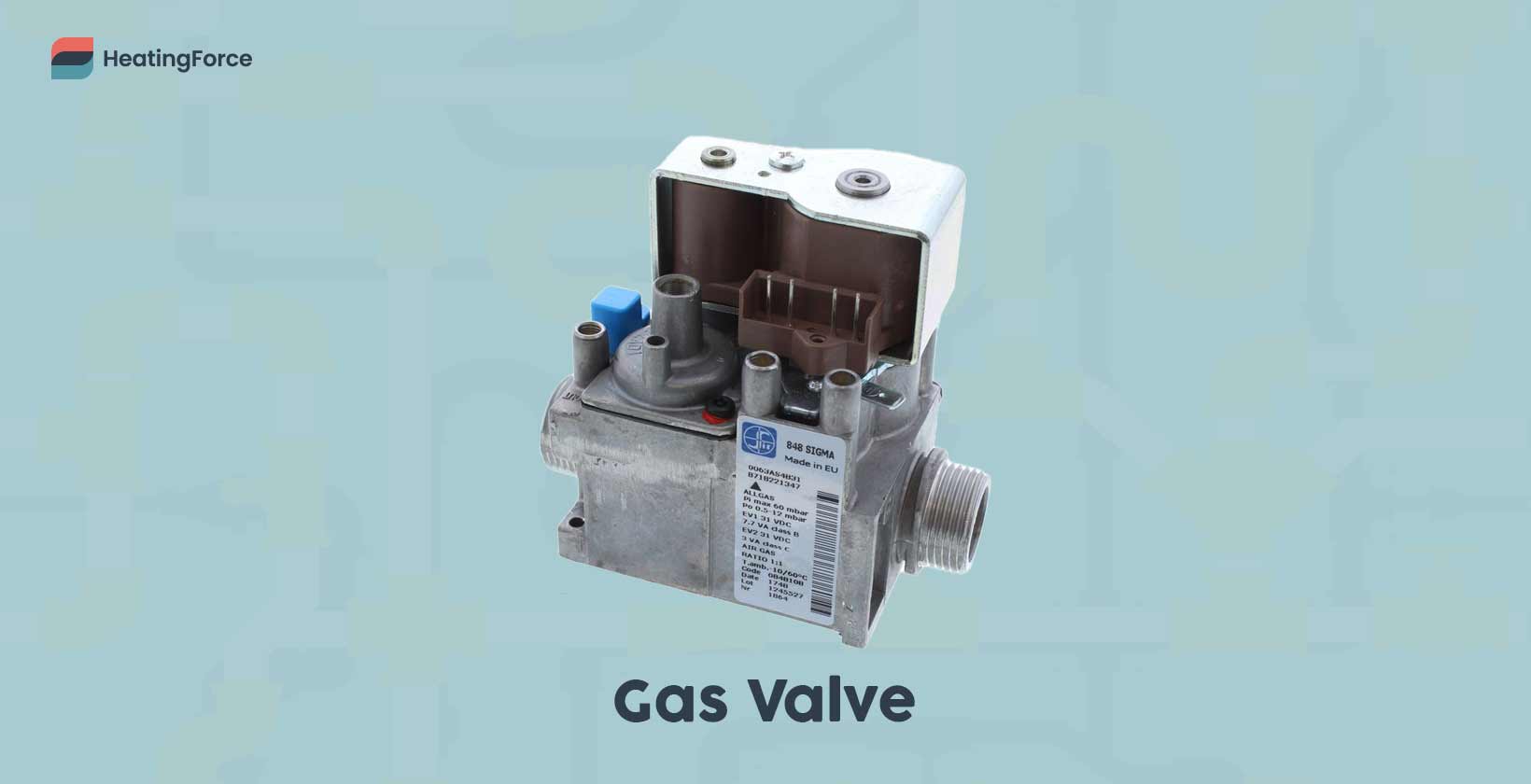
The gas valve regulates the flow of gas into the boiler’s burner for combustion. It ensures the correct amount of gas enters the burner, thus allowing the boiler to operate safely and efficiently. In oil boilers, the oil pump plays a similar role by controlling the delivery of kerosene to the boiler’s burner.
A malfunctioning gas valve may cause issues such as inefficient combustion, higher fuel consumption, or even safety hazards due to gas leaks. In oil boilers, issues with the oil pump likewise lead to inefficient operation and potential breakdowns.
Annual servicing of the gas valve or the oil pump is crucial for the boiler’s longevity and efficiency. Gas valves and oil pumps that are damaged beyond repair generally require prompt replacement, and the cost of buying a new gas valve or oil pump is roughly £120 excluding installation. A Gas Safe engineer should have no trouble procuring a replacement valve for most modern boiler models.
23. Filling loop
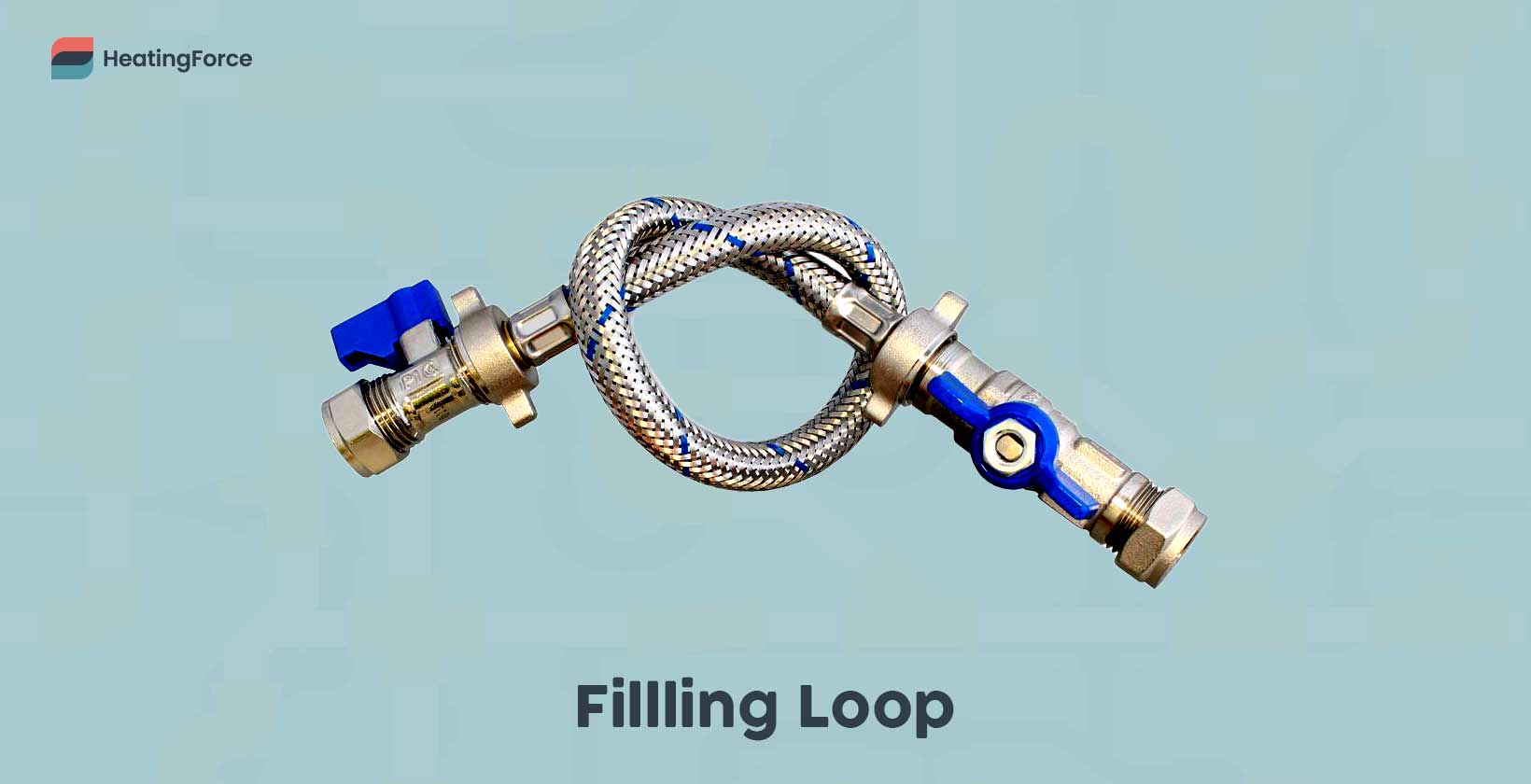
The filling loop allows the user of a sealed-system boiler (i.e. a system or a combi) to repressurise their heating system. The loop connects the boiler to the domestic water supply and allows additional water to enter the heating system.
Regular checks of the boiler’s pressure gauge and the use of the filling loop to adjust pressure are part of routine maintenance. Topping up boiler pressure via the loop is a simple task that ensures the heating system operates effectively. However, note that a boiler that’s losing pressure constantly indicates a leak somewhere in the heating system. You must repair this leak before repressurising the boiler, otherwise, the pressure loss will continue.
The filling loop is a low-cost component, with an average price hovering between £14-£30, excluding labour. New filling loops are easy to find for most modern combi and system boilers.
24. Supply lines
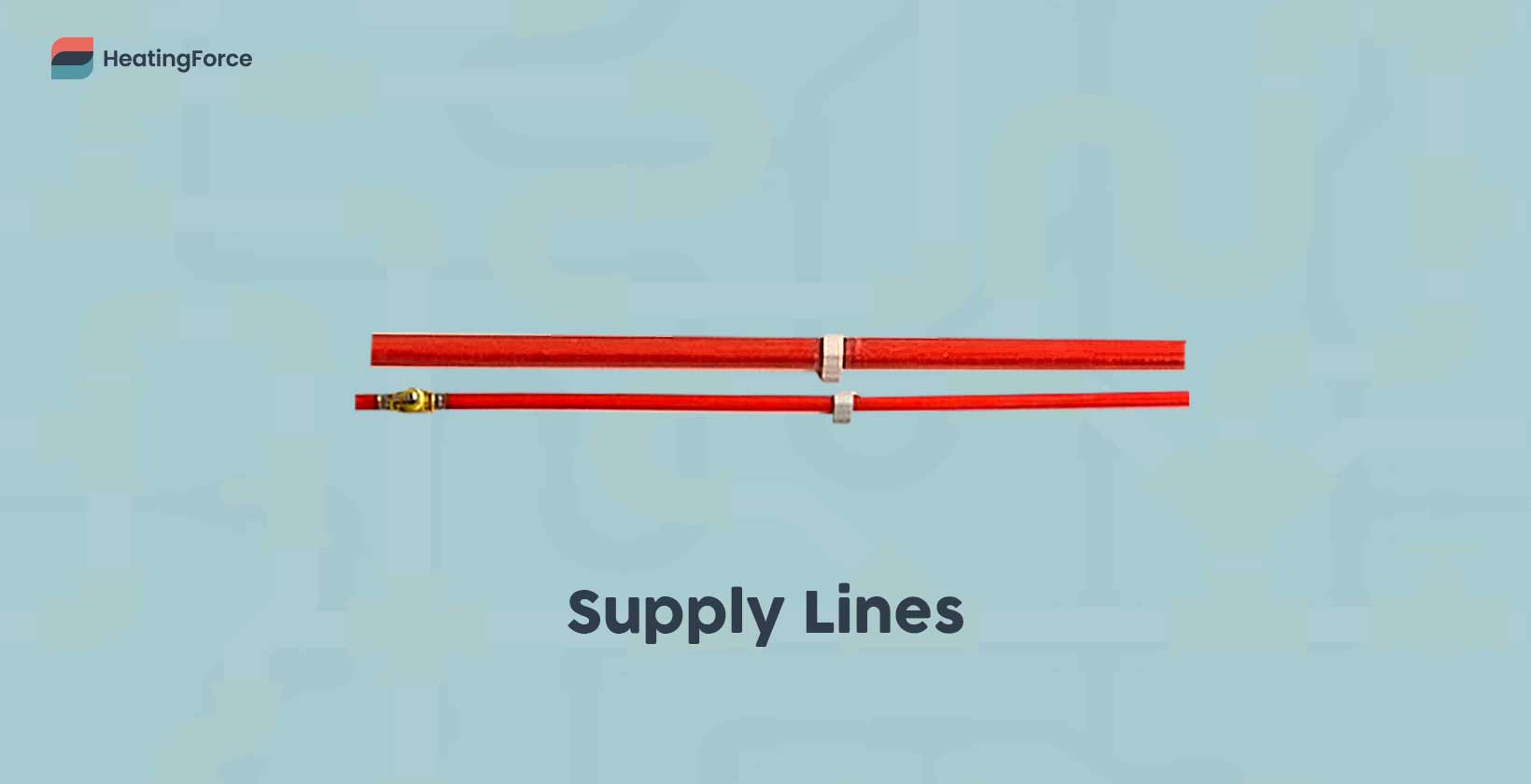
Boiler supply lines are the pipes that deliver heated water to the home’s radiators. The lines must be robust and insulated in accordance with the UK’s pipe insulation guidelines to ensure minimal heat loss. The material of the supply lines must withstand the temperatures and pressures involved in the boiler operation.
Regular maintenance of supply lines includes checking for leaks, corrosion, or damage. Issues with the supply lines may lead to inefficiencies, such as heat loss, or leaks and the resulting damage.
The cost of installing supply lines ranges greatly depending on the configuration of the property and its central heating system. The heating or plumbing technician setting up the system should have no trouble sourcing quality pipes for the supply lines.
25. Return lines
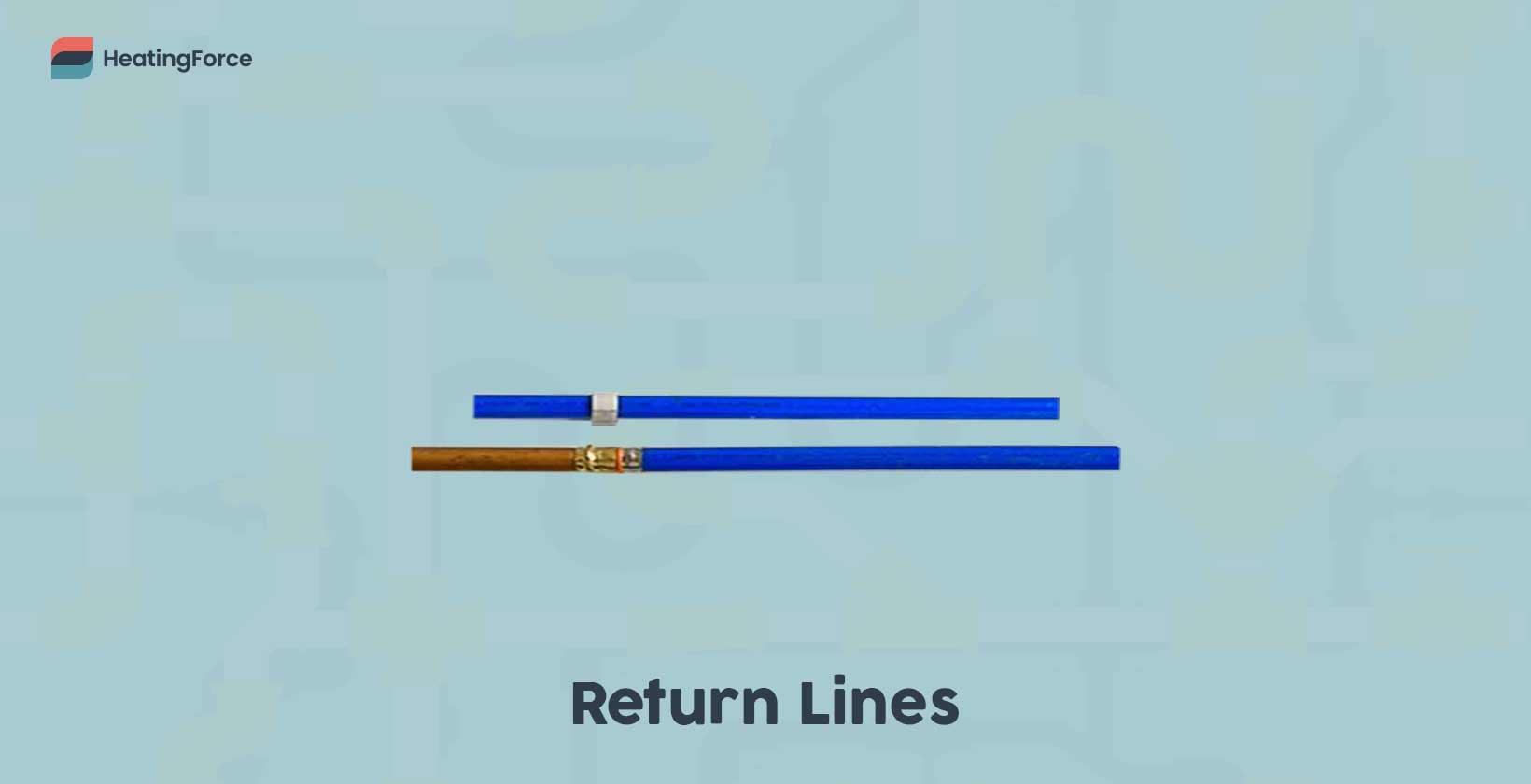
Return lines carry water back to the boiler once it has released heat into the home via radiators, serving the opposite function of the supply lines in a heating system. Like supply lines, return lines need to be sturdy, insulated where required, and free from leaks or blockages to minimise the loss of heat.
The maintenance of return lines involves inspecting for leaks and other damage. Any such issues lead to reduced system efficiency and may result in property damage.
The cost of installing and maintaining return lines hinges on the home’s layout, floor area, and the parameters of the heating system. Replacement pipework is readily available to plumbing and heating engineers installing new heating systems or repairing old ones.
26. Condensate trap and drain
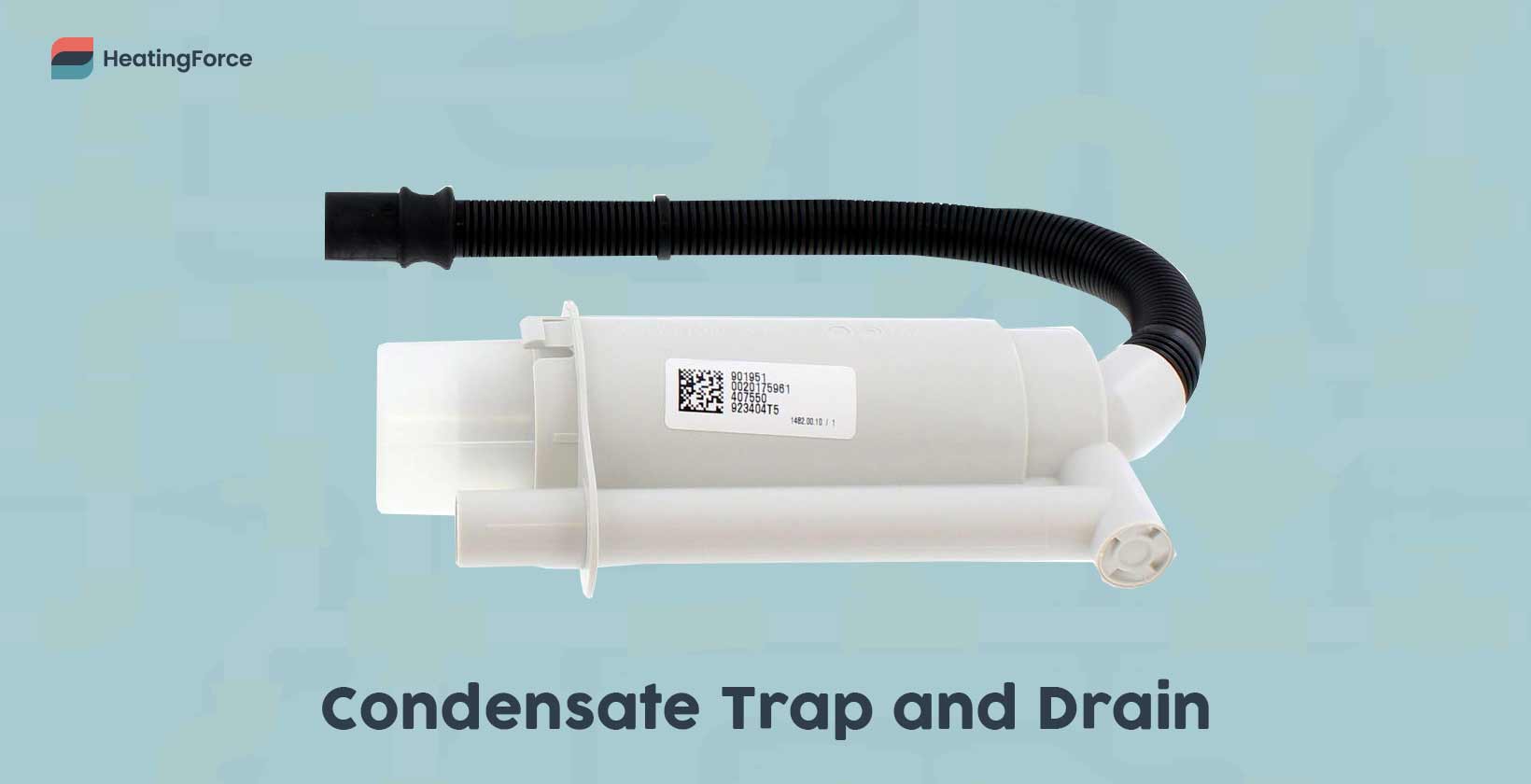
The condensate trap and drain collect and dispose of the acidic condensate produced by the combustion process in modern boilers. The mechanism is designed to collect this acidic water and prevent combustion gases from entering the home. It ensures that only condensate is drained out while keeping harmful gases contained. The condensate then flows from the trap to the drain, which safely carries it away from the boiler and disposes of it, preferably to the internal soil stack or an external drain.
In freezing conditions, the condensate may cause blockages and boiler lockouts by freezing inside the pipe, so proper insulation and routing of the condensate drain are essential. Additionally, adequate regular inspections are vital to maintaining the system’s integrity and function. Replacing a malfunctioning condensate trap and drain typically costs around £60-£100 at local and online boiler part dealers.
How does a boiler work?
A boiler works by heating water in a vessel with a flame produced by burning gas, LPG, or oil, or by passing electricity through a heating element. The main function of a boiler is to generate hot water, which then circulates throughout the home’s radiators and releases heat to raise the indoor air temperature. Additionally, the boiler heats domestic hot water for use in the home’s taps or showers.
Fossil fuel-fired and electric boilers differ in how they produce heat. In gas and oil boilers, fuel burns in a combustion chamber. The heat generated from this combustion transfers to the water in the boiler’s heat exchanger. Meanwhile, electrical heating elements within the vessel raise the water temperature in electric boilers.
What kind of fuel does your boiler use?
Fixed price online with next day installation
There are three primary boiler types, all of which may be fuelled by gas, LPG, oil, or electricity. The three boiler types all have the same primary function of heating water for the home’s radiators and taps. However, they operate in three distinct ways, as outlined in the list below.
- Combination boilers: Combination (commonly known as “combi”) boilers have two heat exchangers. The primary heat exchanger raises the temperature of the central heating water, whilst the secondary heat exchanger warms the water flowing to the home’s taps. Both heat exchangers are contained within the boiler casing, so combi boilers do not require cold or hot water storage tanks.
- System boilers: System boilers have a single heat exchanger, which raises the temperature of the central heating water. This water then flows through a coil inside the hot water cylinder, thus providing indirect heat to the home’s domestic hot water as it circulates through the home’s radiators. System boilers operate with an unvented heating system and must be topped up directly from the mains.
- Regular boilers: Regular boilers operate much like their system boiler counterparts. The only difference between a regular and a system boiler is that the former requires two cold water storage tanks: one to supply DHW to the insulated water cylinder, and the other to maintain the pressure within the heating system.
The efficient operation of a boiler depends on various components working together, regardless of the fuel and boiler type. These include the burner or heating element for heat generation, the heat exchanger for transferring heat to the water, and the circulator pump for moving the heated water through the system. Safety devices such as the pressure release valve and overheat thermostat ensure the system operates within safe limits.
Regular service is vital for a boiler’s efficiency and longevity and should involve checking components like the burner, heat exchanger, circulator pump, and others. Proper care ensures the boiler continues to provide heat and hot water consistently and efficiently.
What component of the boiler is the most important?
All boiler components are important, as the boiler is unable to function properly without all the parts working well together. However, the four parts below are arguably the most important, as the absence of either one of these components would render the boiler inoperable.
- Burner: The burner is an essential boiler component because, without it, the boiler would be left without its source of heat. Without the ability to produce heat, the boiler would not be able to perform its primary function of heating water.
- Heat exchanger: The heat exchanger is integral to the boiler’s function because it allows the heat generated in the burner to transfer to the water. Without a heat exchanger, the boiler would be unable to fulfil its role as a water-heating apparatus.
- PCB: The PCB facilitates communications between the boiler’s components and executes user commands. A boiler would be unable to fire up, produce heat, or respond to any controls without a working PCB present.
- Fan: The fan helps expel toxic exhaust fumes from the boiler and the home. The boiler’s safety mechanisms shut the boiler down and lock it out if the fan is not functioning properly.
- Flue: The flue allows the harmful gases produced in the combustion chamber to escape to the outdoors. Running a boiler without a functioning flue would quickly fill the home with lethal carbon monoxide, endangering the dwellers’ lives and well-being. Issues that prevent a boiler’s flue from operating properly (such as a blockage) typically result in a boiler lockout.
How often should boiler maintenance occur?
Boiler maintenance must occur every year. Regular boiler servicing is key to ensuring the boiler operates safely and efficiently and is typically a requirement to keep the boiler’s warranty valid.
Annual boiler service involves a qualified Gas Safe or OFTEC engineer inspecting various components of the boiler, such as the burner, heat exchanger, and circulator pump. These checks include ensuring the combustion process is efficient and safe, with no risk of carbon monoxide leaks. With electric boilers, the maintenance focus is on electrical connections and heating elements. The inspecting engineers additionally clean and adjust parts as needed.
Boiler service may uncover a wide array of faults with the boiler’s internal components. Some of these may be repaired quickly and without added expenses for the owner if the part is covered under the boiler warranty. However, severely damaged, irreparable components may require a full replacement. If the boiler is no longer under warranty and several of its essential components are beyond repair, installing a brand-new boiler may be the most sensible solution for the owner.
Heatable’s online boiler calculator is an excellent place to start comparing prices for new boilers. All you need to do is fill in an anonymous property questionnaire and Heatable will generate a range of fixed-price quotes on new boilers from the nation’s best manufacturers.
No Fuss.
Get your fixed online price for a Which? approved boiler, installation included.
What part of the boiler requires regular maintenance?
Below are the seven components of a boiler that require regular maintenance.
- Burner: The burner must be cleaned and checked for proper functioning. A well-maintained burner ensures efficient fuel combustion, which is essential for energy efficiency and safety.
- Heat exchanger: This component requires inspection for signs of corrosion, blockages, or leaks. A clean and intact heat exchanger is crucial for efficient heat transfer and overall boiler efficiency.
- Flue/exhaust stack: The flue should be checked for blockages or leaks to ensure harmful gases are safely vented outside.
- Safety devices: Checking the safety devices involves testing the pressure release valve and overheat thermostat.
- Circulator pump: The pump should be inspected for leaks and tested to ensure it’s able to circulate heated water properly.
- Condensate trap and drain: The inspecting engineer must check the condensate trap and drain for blockages to avert the risk of freezing in cold weather.
- Controls and timers: Boiler controls and timers require testing for accuracy and functionality to ensure they respond correctly to user commands.
- Filters (if applicable): Any filters should be cleaned or replaced during boiler service to maintain efficient operation.
Annual boiler service by a qualified engineer helps keep the boiler’s crucial components in good working order, ensuring the heating system functions safely and efficiently.
Does negligence in maintenance cause common boiler problems?
Yes, negligence in maintenance causes common boiler problems. Below are five common problems caused by negligent boiler maintenance.
- Decreased efficiency: Components such as burners and heat exchangers may become less efficient without thorough cleaning and accurate adjustments. A loss of efficiency leads to increased fuel consumption and higher energy bills.
- Breakdowns: Neglecting routine checks leads to wear and tear on various parts, increasing the likelihood of breakdowns and costly repairs.
- Safety hazards: Failing to maintain safety components like the pressure release valve or overheat thermostat may lead to dangerous situations, such as carbon monoxide leaks.
- Shortened lifespan: Regular maintenance extends the life of a boiler while neglecting the boiler leads to its early deterioration and the need for premature replacement.
- Invalid warranty: Many manufacturers require annual servicing as a condition of their warranty, and neglecting annual boiler service generally voids the warranty.
How do different types of boilers differ in parts?
Combi, system, and regular boilers differ in their components and how they operate within a heating system. The list below overviews the six key components that vary between the three different types of boilers.
- Secondary heat exchanger: Combi boilers have a secondary heat exchanger for heating domestic water. Meanwhile, system and regular boilers only heat water for radiators, and so do not require a secondary heat exchanger.
- Expansion vessel: Combi and system boilers operate within a sealed system, meaning that there is no external pressure outlet within the heating system. As such, these two boiler types require an expansion vessel to accommodate the expansion of water volume due to heat. Meanwhile, regular boilers rely on a feed-and-expansion tank to handle changes in water pressure and volume and so do not need an integral expansion vessel.
- Circulator pump: Combi and system boilers typically have an integral circulator pump that facilitates water flow throughout the home’s pipes and radiators. On the other hand, regular boilers work with an external pump that’s connected to the pipework.
- Diverter valve: Combi boilers have a diverter valve that allows them to switch between heating and domestic hot water modes. In contrast, system and regular boilers only operate in the heating mode and thus do not require a diverter valve.
- Hot water cylinder: System and regular boilers are unable to heat potable water on demand the way combis do. Instead, they indirectly heat DHW that’s stored inside an insulated cylinder.
- Cold water storage tank: Conventional boiler setups operate with a cold water storage tank that feeds the domestic hot water cylinder. Meanwhile, system boilers’ cylinders get topped up right from the mains and combi boilers draw water from the mains upon demand from the user.
Do boiler parts affect the choice of boiler type?
Yes, the boiler parts affect the choice of boiler type. Below are three examples of how boiler parts may dictate one’s choice of boiler type.
- Space considerations: Combi boilers lack external tanks or cylinders, and are thus ideal for smaller homes or areas where space is at a premium. Conversely, system and regular boilers take up a greater floor area due to their cold and hot water storage tanks.
- Water consumption: Homes with higher water usage (especially those with multiple bathrooms) benefit from having a cylinder to keep a large volume of hot water ready. System and regular boilers are able to work with such cylinders, whilst combis are not.
- Existing heating system: Compatibility with the existing heating system in a home may dictate the choice of boiler type. For example, installing a new regular boiler is the simplest and least expensive solution in a home with a traditional heating configuration.
If you’re not sure which boiler type is most suitable for your home, use Heatable’s online boiler selection tool to get a professional recommendation. The selection tool takes into account your property configuration and heating needs to recommend a range of new boiler models along with fixed-price quotes right on your screen.